Method for thermally replacing furnace bottom of high-flow top-bottom combined blown converter
A top-bottom re-blowing, high-flow technology, applied in the direction of manufacturing converters, etc., can solve the problems of loss of re-blowing effect and bottom blowing shutdown, and achieve the effect of improving converter operation rate, reducing occupied time, and reducing production costs.
- Summary
- Abstract
- Description
- Claims
- Application Information
AI Technical Summary
Problems solved by technology
Method used
Image
Examples
Embodiment Construction
[0031] The following examples are used to illustrate the present invention, but are not intended to limit the scope of the present invention. Unless otherwise specified, the examples are all in accordance with conventional experimental conditions. In addition, for those skilled in the art, on the premise of not departing from the spirit and scope of the present invention, various modifications or improvements to the material components and dosage in these embodiments all belong to the protection scope of the present invention.
[0032] Such as figure 1 A method for thermally replacing the furnace bottom of a large-flow top-bottom compound-blowing converter shown includes the following steps:
[0033] S1. Furnace shutdown: When the erosion thickness of the bottom of the large-flow top-bottom combined blowing furnace reaches the replacement standard, the furnace is shut down to prepare for hot replacement of the old bottom; There is no need for slag splashing to protect the fu...
PUM
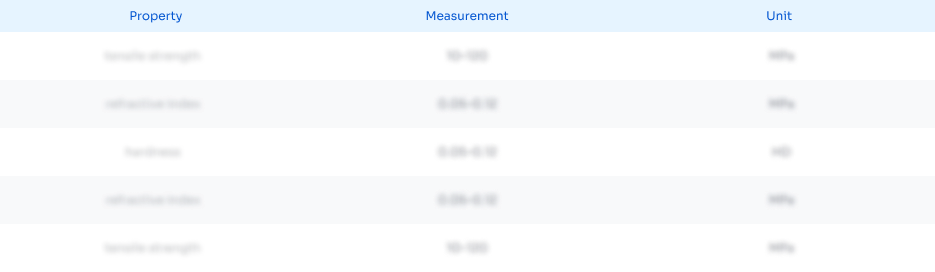
Abstract
Description
Claims
Application Information

- R&D Engineer
- R&D Manager
- IP Professional
- Industry Leading Data Capabilities
- Powerful AI technology
- Patent DNA Extraction
Browse by: Latest US Patents, China's latest patents, Technical Efficacy Thesaurus, Application Domain, Technology Topic, Popular Technical Reports.
© 2024 PatSnap. All rights reserved.Legal|Privacy policy|Modern Slavery Act Transparency Statement|Sitemap|About US| Contact US: help@patsnap.com