Method for optimizing machining sequence of aluminum alloy component based on computer simulation and computer equipment
A technology of aluminum alloy components and computer simulation, applied in design optimization/simulation, special data processing applications, instruments, etc., can solve problems such as unreliable simulation results and unreasonable process optimization of simulation results, so as to reduce trial and error costs, reduce The effect of trial production cycle
- Summary
- Abstract
- Description
- Claims
- Application Information
AI Technical Summary
Problems solved by technology
Method used
Image
Examples
Embodiment approach 1
[0051] Embodiment 1, a method for optimizing the machining sequence of aluminum alloy components based on computer simulation, the method includes:
[0052] Obtain the material parameters of the component blank;
[0053] Obtaining a three-dimensional model of the component blank after cutting according to the engineering drawing of the component;
[0054] Meshing the cut three-dimensional model;
[0055] Performing heat treatment simulation on the three-dimensional model after the grid division according to the material parameters, and obtaining the stress field distribution and deformation field distribution of the model after the heat treatment simulation;
[0056] According to the stress field distribution and the deformation field distribution of the model after the heat treatment simulation, the machining simulation is performed on the three-dimensional model after the heat treatment simulation, and the stress field distribution and the deformation field distribution of ...
Embodiment approach 2
[0060] Embodiment 2. This embodiment is a further limitation of the method for optimizing the machining sequence of aluminum alloy components based on computer simulation described in Embodiment 1. In this embodiment, the material parameters are further limited, and the Material parameters include, but are not limited to: density, coefficient of thermal expansion, specific heat capacity, thermal conductivity, modulus of elasticity, Poisson's ratio, and yield strength.
[0061] It should be noted that the following physical parameters of materials need to be used in the simulation process of components: density, thermal expansion coefficient, specific heat capacity, thermal conductivity, elastic modulus, Poisson's ratio and yield strength. In this embodiment, the accuracy of the simulation result can be ensured by testing the physical parameters of the material at different temperatures.
Embodiment approach 3
[0062] Embodiment 3. This embodiment is a further limitation of the method for optimizing the machining sequence of aluminum alloy components based on computer simulation described in Embodiment 1. In this embodiment, the step of obtaining the material parameters of the component blank is done. Further restrictions include:
[0063] Determination of density, thermal expansion coefficient, specific heat capacity, thermal conductivity, elastic modulus, Poisson's ratio and yield strength;
[0064] Obtain the billet creep constitutive relation through creep test;
[0065] Obtain the billet constitutive relationship through thermal compression experiments;
[0066] The boundary conditions of heat treatment process are determined by multi-point temperature measurement of structural components.
[0067] This embodiment provides the acquisition method of the material parameter of the component blank. It should be noted that the acquisition method can select different methods to acqu...
PUM
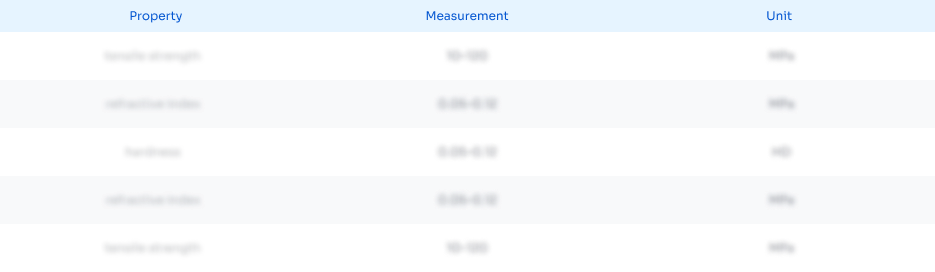
Abstract
Description
Claims
Application Information

- R&D
- Intellectual Property
- Life Sciences
- Materials
- Tech Scout
- Unparalleled Data Quality
- Higher Quality Content
- 60% Fewer Hallucinations
Browse by: Latest US Patents, China's latest patents, Technical Efficacy Thesaurus, Application Domain, Technology Topic, Popular Technical Reports.
© 2025 PatSnap. All rights reserved.Legal|Privacy policy|Modern Slavery Act Transparency Statement|Sitemap|About US| Contact US: help@patsnap.com