Finish machining process of stator and rotor for automobile engine
A technology of automobile engines and stators and rotors, which is applied in the direction of manufacturing tools and other manufacturing equipment/tools. It can solve the problems of inconvenient and quick replacement, affecting the normal operation of the transmission structure on the machine tool, and deepening the wear of the rotating parts of the machine tool, so as to ensure the finishing process. efficiency effect
- Summary
- Abstract
- Description
- Claims
- Application Information
AI Technical Summary
Problems solved by technology
Method used
Image
Examples
Embodiment 1
[0053] Example 1, as Figure 2-4 As shown, before finishing the stator and rotor, the operator passes the hand through the square through hole and turns a set of handwheels 803 close to the door of the processing chamber 1 counterclockwise, and uses the screw thread to force the threaded rod 805 to approach the first servo motor One end of 6 moves, and drives the rotating plate 801 to approach the first servo motor 6 together, the distance between the rotating plate 801 and the rotating deck 9 increases, and then the operator manually inserts one end of the stator and rotor into the concave of the rotating deck 9 slot, and turn the hand wheel 803 clockwise to allow the other end of the stator and rotor to snap into the slot 806, thereby installing the stator and rotor for subsequent finishing of the stator and rotor, and replacing the finished stator and rotor , then turn the hand wheel 803 clockwise to drive the threaded rod 805 to rotate clockwise, allowing the rotating plat...
Embodiment 2
[0054] Example 2, such as Figure 1-10 As shown, when the device is finishing the stator and rotor, the second servo motor 24 is first controlled to rotate clockwise through the control panel 3, and the transmission of the driving gear 11 and the second ring rack 19 is used to drive the two groups of turntables 13 to reverse each time. The hour hand rotates 90°, so that the stator and rotor pass through the bottom of the grinding device 2 first, then pass through one side of the turning assembly 7 and the top of the rotating ring 125, and when the turntable 13 stops, the first servo motor 6 drives the rotating chamber 14 rotates, and the rotating chamber 14 drives the three groups of rotating decks 9 to rotate synchronously through the driving gear 18 on the first rotating tube 17 and the three groups of transmission gears 23, thereby driving the three groups of stators and rotors to rotate synchronously, and the grinding device 2 is used to pair the stators and rotors Grindin...
Embodiment 3
[0055] Example 3, such as Figure 2-6 As shown in and 9-10, when dust is removed inside the processing chamber 1, the air pump 105 is controlled by the control panel 3 to suck air, and the metal dust generated by the grinding device 2 is mixed with air and enters the rotating chamber 14 through the air inlet 15 Afterwards, the metal dust and air enter the interior of the filter chamber 102 through the first rotating tube 17, and the metal dust will be filtered and blocked by three sets of filter screens 101. After the filtered air passes through the heat exchange tube 104, it is pumped The air pump 105 is transported to the inside of the air pipe 106, and the filtered air is finally sprayed out through the nozzle 107, and the surface of a group of stators and rotors at the bottom is blown to cool down, so that the processed stators and rotors can be quickly replaced, and the nozzle 107 sprays out The air in the air will also blow and remove dust on the surface of the set of st...
PUM
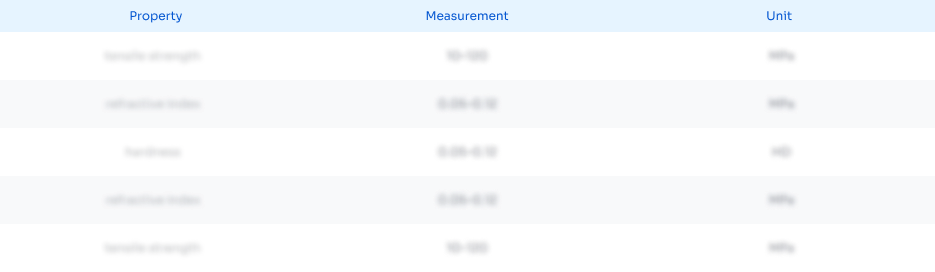
Abstract
Description
Claims
Application Information

- R&D Engineer
- R&D Manager
- IP Professional
- Industry Leading Data Capabilities
- Powerful AI technology
- Patent DNA Extraction
Browse by: Latest US Patents, China's latest patents, Technical Efficacy Thesaurus, Application Domain, Technology Topic.
© 2024 PatSnap. All rights reserved.Legal|Privacy policy|Modern Slavery Act Transparency Statement|Sitemap