Method for enhancing mechanical property of electrospun fibrous membrane
A technology of electrospinning fiber and mechanics, which is applied in the field of nanomaterial preparation, can solve the problems of poor mechanical properties of electrospun nanofiber membranes, affect the porosity of fiber membranes, reduce the purity of fiber membranes, etc., and achieve enhanced mechanical properties and controllability High, good enhancement effect
- Summary
- Abstract
- Description
- Claims
- Application Information
AI Technical Summary
Problems solved by technology
Method used
Image
Examples
Embodiment 1
[0036] Dissolve polyvinylidene fluoride in a mixed solvent of N,N-dimethylformamide (DMF) and acetone (Ace) with a volume ratio of 3:1, and prepare a spinning solution with a mass volume ratio of 25% as a dense layer Spinning solution and non-woven layer spinning solution. Dissolve polylactic acid-glycolic acid copolymer in a mixed solvent with a volume ratio of N,N-dimethylformamide (DMF) and acetone (Ace) of 9:1, and prepare a spinning solution with a mass volume ratio of 47%. As an adhesive layer spinning solution. In the electrospinning process, the drum was used as the receiving device to prepare the electrospun fiber membrane. In the first electrospinning process and the third electrospinning process, the spinning receiving distance was 30 cm; in the second electrospinning process , the receiving distance is set to 12cm. Thus, a three-layer electrospun fiber membrane was obtained based on the addition of an adhesive layer to cause adhesion between the fiber layer and t...
Embodiment 2
[0038] Dissolve polylactic acid in a mixed solvent of N,N-dimethylformamide (DMF) and dichloromethane (DCM) with a volume ratio of 1:4, and prepare a spinning solution with a mass volume ratio of 20% as a dense layer Spinning solution and non-woven layer spinning solution. Dissolve polylactic acid-glycolic acid copolymer in a mixed solvent of N,N-dimethylformamide (DMF) and acetone (Ace) with a volume ratio of 5:1, and prepare a spinning solution with a mass volume ratio of 45%. As an adhesive layer spinning solution. In the electrospinning process, the drum was used as the receiving device to prepare the electrospun fiber membrane. In the first electrospinning process and the third electrospinning process, the spinning receiving distance was 25 cm; in the second electrospinning process , set the spinning receiving distance to 16cm. Thus, a three-layer electrospun fiber membrane was obtained based on the addition of an adhesive layer to cause adhesion between the fiber layer...
Embodiment 3
[0040]Poly L-lactide-co-caprolactone is dissolved in hexafluoroisopropanol (HFIP) and dichloromethane (DCM) in the mixed solvent that the volume ratio is 1:1, is prepared as the mass volume ratio is 20% The spinning solution is used as a dense layer spinning solution and a non-woven layer spinning solution. Dissolve polylactic acid-glycolic acid copolymer in a mixed solvent of N,N-dimethylformamide (DMF) and acetone (Ace) with a volume ratio of 3:1, and prepare a spinning solution with a mass volume ratio of 47%. As an adhesive layer spinning solution. In the electrospinning process, the drum was used as the receiving device to prepare the electrospun fiber membrane. In the first electrospinning process and the third electrospinning process, the spinning receiving distance was 28 cm; in the second electrospinning process , set the spinning acceptance distance to 5 cm. Thus, a three-layer electrospun fiber membrane was obtained based on the addition of an adhesive layer to ca...
PUM
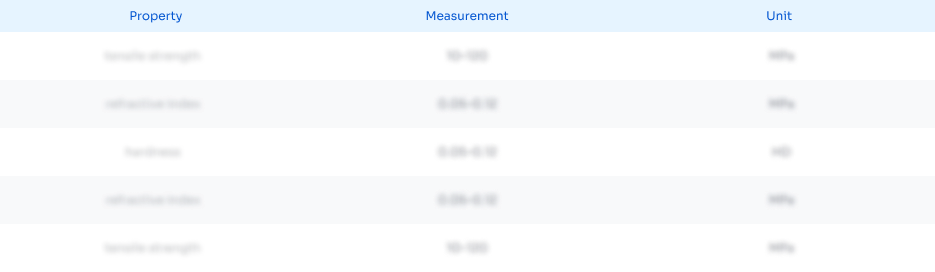
Abstract
Description
Claims
Application Information

- R&D
- Intellectual Property
- Life Sciences
- Materials
- Tech Scout
- Unparalleled Data Quality
- Higher Quality Content
- 60% Fewer Hallucinations
Browse by: Latest US Patents, China's latest patents, Technical Efficacy Thesaurus, Application Domain, Technology Topic, Popular Technical Reports.
© 2025 PatSnap. All rights reserved.Legal|Privacy policy|Modern Slavery Act Transparency Statement|Sitemap|About US| Contact US: help@patsnap.com