Steel slag treatment technology and application of tailings obtained by steel slag treatment process
A treatment process and technology for steel slag, which is applied in the application field of steel slag treatment process and its resulting tailings, which can solve the difficulty of visible pollution control on site of dry grinding and dry separation, high control index of free calcium oxide, and uneven control of material particle size To achieve the effect of avoiding groundwater pollution, improving the grade and recovery rate of magnetic substances, and improving benefits
- Summary
- Abstract
- Description
- Claims
- Application Information
AI Technical Summary
Problems solved by technology
Method used
Image
Examples
Embodiment 1
[0033] A production process for road surface layer steel slag in alpine regions, comprising the following steps:
[0034] 1) steel slag is carried out pre-treatment, and described pre-treatment comprises heat-splashing treatment and heap stewing;
[0035] 2) The steel slag obtained after the pretreatment in step 1) is sieved by a drum sieve after three-stage crushing:
[0036] The material with a particle size of ≤8mm is directly subjected to multi-stage magnetic separation, the magnetic material is the final product steel fine powder, and the non-magnetic material is the final product tailings;
[0037] The material with a particle size > 8mm enters the rod mill for re-crushing, and the crushed material is screened again with a drum sieve, and the material with a particle size > 8mm is sorted by a magnetic separator. The magnetic material is the final product particle steel, and the non-magnetic material is recycled. Enter the rod mill.
[0038] In this embodiment, during t...
Embodiment 2
[0044] A production process for road surface layer steel slag in alpine regions, comprising the following steps:
[0045] 1) steel slag is carried out pre-treatment, and described pre-treatment comprises heat-splashing treatment and heap stewing;
[0046] 2) The steel slag obtained after the pretreatment of step 1) is sieved after three-stage crushing:
[0047] The material with a particle size of ≤8mm is directly subjected to multi-stage magnetic separation, the magnetic material is the final product steel fine powder, and the non-magnetic material is the final product tailings;
[0048] Materials with a particle size > 8mm enter the rod mill for re-crushing, and the crushed materials are screened again. Materials with a particle size > 8mm are sorted by a magnetic separator. The magnetic material is the final product particle steel, and the non-magnetic material circulates into the rod mill. machine.
[0049] In this embodiment, the stacking and stewing process adopts the ...
PUM
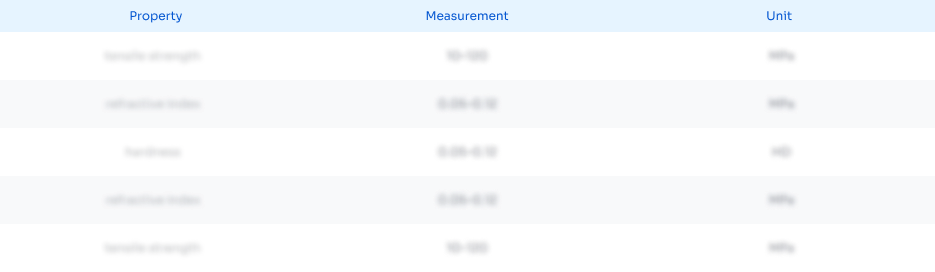
Abstract
Description
Claims
Application Information

- R&D Engineer
- R&D Manager
- IP Professional
- Industry Leading Data Capabilities
- Powerful AI technology
- Patent DNA Extraction
Browse by: Latest US Patents, China's latest patents, Technical Efficacy Thesaurus, Application Domain, Technology Topic, Popular Technical Reports.
© 2024 PatSnap. All rights reserved.Legal|Privacy policy|Modern Slavery Act Transparency Statement|Sitemap|About US| Contact US: help@patsnap.com