Micro-stress combined machining method for aero-engine turbine disc mortise
An aero-engine and composite processing technology, applied in metal processing equipment, metal processing mechanical parts, manufacturing tools, etc., can solve the problem of difficult to guarantee the size of tenon teeth, achieve high processing accuracy, reduce processing costs, and have obvious economic and national defense effects. Effect
- Summary
- Abstract
- Description
- Claims
- Application Information
AI Technical Summary
Problems solved by technology
Method used
Image
Examples
Embodiment Construction
[0021] The present invention will be described in further detail below in conjunction with the accompanying drawings and specific embodiments.
[0022] In this embodiment, the steps of using the technical solution of the present invention to carry out micro-stress composite machining of the tenon and groove of the turbine disk are as follows:
[0023] Step 1. The wire cutting process in this processing method is completed by numerical control wire cutting equipment and molybdenum wire. According to the structure and size of the turbine disk 2, the clamping method of the turbine disk 2 is determined as follows: figure 1 , 2 As shown, the mounting seat 1 for installing the turbine disk blank 2 is connected to the turntable 6, and the wheel disk blank 2 is fixed by the pressing block 3 and the screw 4, and it is ensured that figure 2 The angle φ in is complementary to the included angle between the tenon groove of the turbine disk and the radial direction;
[0024] In the wire...
PUM
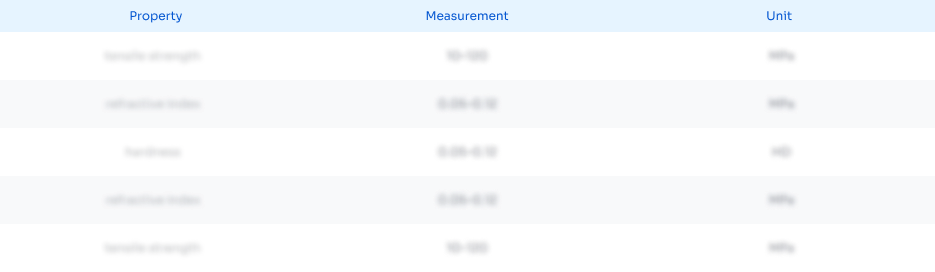
Abstract
Description
Claims
Application Information

- R&D
- Intellectual Property
- Life Sciences
- Materials
- Tech Scout
- Unparalleled Data Quality
- Higher Quality Content
- 60% Fewer Hallucinations
Browse by: Latest US Patents, China's latest patents, Technical Efficacy Thesaurus, Application Domain, Technology Topic, Popular Technical Reports.
© 2025 PatSnap. All rights reserved.Legal|Privacy policy|Modern Slavery Act Transparency Statement|Sitemap|About US| Contact US: help@patsnap.com