Lignin separation system and method thereof
A separation system and technology for lignin, applied in separation methods, filtration separation, chemical instruments and methods, etc., can solve the problems of low production efficiency and high requirements for separation conditions, and achieve simple equipment, easy large-scale industrialization, and low production costs. Effect
- Summary
- Abstract
- Description
- Claims
- Application Information
AI Technical Summary
Problems solved by technology
Method used
Image
Examples
Embodiment 1
[0035] Such as figure 1 As shown, this embodiment discloses a lignin separation system, including a reaction kettle 1, a solvent tank 2, a lignin separation tank 3, a first filter press 4, a water tank 5, a solvent / water tank 6, a solvent buffer tank 7, An air compressor 8, an air storage tank 9, a second filter press 10, and a high-efficiency evaporator 11.
[0036] Such as figure 1 As shown, the reaction kettle 1 of the present embodiment is provided with a raw material inlet 101, a solid-liquid outlet, a compressed air inlet, a water inlet, a first solvent inlet / outlet, a second solvent inlet, a first solvent outlet / inlet and a second solvent outlet. Two solvent outlets, the raw material inlet 101 are connected with the external conveyor belt.
[0037]Such as figure 1 As shown, the solvent tank 2 of this embodiment includes two tanks, specifically the first solvent tank 201 and the second solvent tank 202, and the first solvent tank 201 and the second solvent tank 202 ar...
Embodiment 2
[0063] The method for separating lignin by a lignin separation system comprises the following steps:
[0064] a. Crush the rice straw to less than 1.5 cm, take 200 kg and pour it into the reaction kettle 1 through the conveyor belt from the raw material inlet 101;
[0065] B, add 800 kilograms of ethylene glycol and 10 kilograms of p-toluenesulfonic acid in the first solvent tank 201, draw into reactor 1 after stirring evenly, and flow to the second solvent tank 202 from reactor 1, reactor 1 simultaneously Heating to 80°C, when the solvent in the first solvent tank 201 is exhausted, the solvent is drawn into the reaction kettle 1 from the second solvent tank 202, and flows to the first solvent tank 201, repeating this many times until the lignin is basically dissolved Finally, stop pumping the solvent so that the solvent completely enters the first solvent tank 201 and the second solvent tank 202;
[0066] c. Add ethylene glycol in the solvent buffer tank 7, and pump it into ...
Embodiment 3
[0072] The difference between this embodiment and the second embodiment is that in step a, the rice stalks are replaced with corn stalks.
[0073] The lignin extraction rate obtained by using the method of this embodiment exceeds 93%, and ethylene glycol, water and remaining p-toluenesulfonic acid are recycled.
PUM
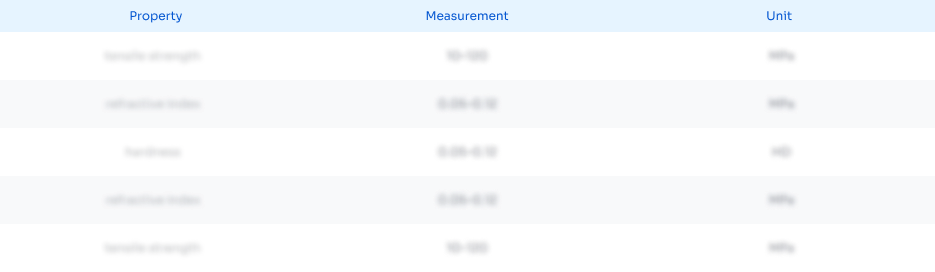
Abstract
Description
Claims
Application Information

- R&D
- Intellectual Property
- Life Sciences
- Materials
- Tech Scout
- Unparalleled Data Quality
- Higher Quality Content
- 60% Fewer Hallucinations
Browse by: Latest US Patents, China's latest patents, Technical Efficacy Thesaurus, Application Domain, Technology Topic, Popular Technical Reports.
© 2025 PatSnap. All rights reserved.Legal|Privacy policy|Modern Slavery Act Transparency Statement|Sitemap|About US| Contact US: help@patsnap.com