Efficient milling parameter optimization method for rough machining of difficult-to-machine material fused with tool wear monitoring
A tool wear and difficult-to-machine technology, applied in the direction of electrical digital data processing, CAD numerical modeling, special data processing applications, etc., can solve the problems of little consideration, lack of physical properties, and inability to accurately judge the state of the tool, so as to improve the application capacity, large material removal rate, and improved search capability
- Summary
- Abstract
- Description
- Claims
- Application Information
AI Technical Summary
Problems solved by technology
Method used
Image
Examples
Embodiment Construction
[0138] The present invention will be described in detail below in conjunction with the accompanying drawings and embodiments.
[0139] An efficient milling parameter optimization method for rough machining of difficult-to-machine materials combined with tool wear monitoring, comprising the following steps:
[0140] Step 1) Establish a characterization model for optimization problems with machining efficiency as the goal, spindle speed, radial width of cut, and axial depth of cut as optimization variables, and consideration of multiple constraints such as the feasible region of basic parameters, stability, spindle torque, and power ;
[0141] 1.1) Establish optimization goals:
[0142] refer to figure 1, the typical milling process is often used in the rough machining of parts; the goal of milling rough machining parameters optimization is to maximize the machining efficiency under the relevant constraints; the constraints here include the feasible range of basic milling para...
PUM
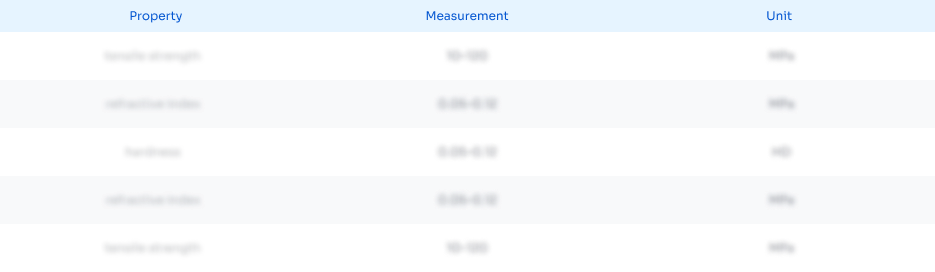
Abstract
Description
Claims
Application Information

- Generate Ideas
- Intellectual Property
- Life Sciences
- Materials
- Tech Scout
- Unparalleled Data Quality
- Higher Quality Content
- 60% Fewer Hallucinations
Browse by: Latest US Patents, China's latest patents, Technical Efficacy Thesaurus, Application Domain, Technology Topic, Popular Technical Reports.
© 2025 PatSnap. All rights reserved.Legal|Privacy policy|Modern Slavery Act Transparency Statement|Sitemap|About US| Contact US: help@patsnap.com