Power assembly intelligent thermal management control method and system, and storage medium
A technology of intelligent thermal management and powertrain, applied in the direction of control/regulation system, non-electric variable control, lubricant temperature control, etc., can solve the problem of not being able to control engine operation according to engine working conditions, and not being able to take into account transmission cooling and Inconsistencies in heating demand and required flow changes, etc., to achieve the effects of reducing fuel consumption and emissions, reducing friction loss, and reducing the tendency of knocking
- Summary
- Abstract
- Description
- Claims
- Application Information
AI Technical Summary
Problems solved by technology
Method used
Image
Examples
Embodiment Construction
[0027] The technical solutions implemented by the present invention will be further described below in conjunction with the accompanying drawings in the specification. The described embodiments are only part of the embodiments of the present invention. All other embodiments obtained under the labor premise all belong to the protection scope of the present invention.
[0028] figure 1 is a flowchart of a thermal management control method according to an embodiment of the present invention. This embodiment provides a thermal management control method for an engine, such as figure 1 As shown, the thermal management method may generally include the following steps:
[0029] S10: Data collection, including cylinder head outlet water temperature, cylinder body outlet water temperature, HVAC demand, ambient temperature, intake air temperature, engine oil temperature, transmission oil temperature, vehicle speed, TMM main opening, TMM cylinder head opening and electronic Main water ...
PUM
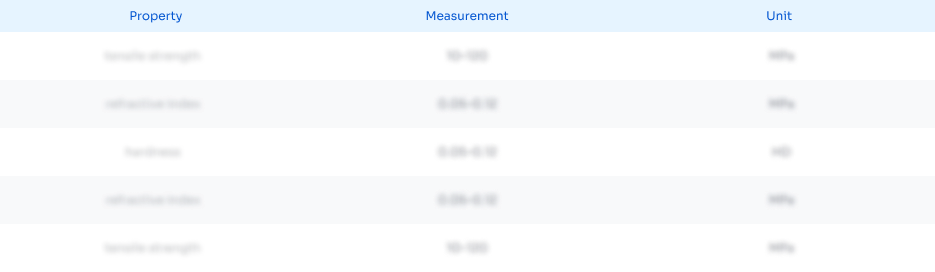
Abstract
Description
Claims
Application Information

- R&D
- Intellectual Property
- Life Sciences
- Materials
- Tech Scout
- Unparalleled Data Quality
- Higher Quality Content
- 60% Fewer Hallucinations
Browse by: Latest US Patents, China's latest patents, Technical Efficacy Thesaurus, Application Domain, Technology Topic, Popular Technical Reports.
© 2025 PatSnap. All rights reserved.Legal|Privacy policy|Modern Slavery Act Transparency Statement|Sitemap|About US| Contact US: help@patsnap.com