Release film compounding equipment and release film compounding production line
A composite equipment, release film technology, applied in the direction of layered products, lamination devices, winding strips, etc., can solve the problems of difficult debugging, complex die parameters, easy peeling, etc., to avoid being easily stretched and deformed , Improve the composite quality and ensure the effect of the final quality
- Summary
- Abstract
- Description
- Claims
- Application Information
AI Technical Summary
Problems solved by technology
Method used
Image
Examples
Embodiment Construction
[0040] The present invention will be described in detail below in conjunction with specific embodiments. The following examples will help those skilled in the art to further understand the present invention, but do not limit the present invention in any form.
[0041] combine figure 1 As shown, the release film composite equipment of the present invention includes a frame; the frame is provided with a first unwinding device, a second unwinding device, an infrared preheating roller 10, a high temperature water preheating roller 6, a composite roller device, a supply Thermal system, cooling roll, third flattening roll 53, trimming mechanism 14 and winding device; the film on the first unwinding device is preheated by infrared preheating roller 10, and the base film on the second unwinding device passes through The high-temperature water preheating roller 6 is used for preheating, and the preheated film and the base film are compounded by a composite roller device to obtain a co...
PUM
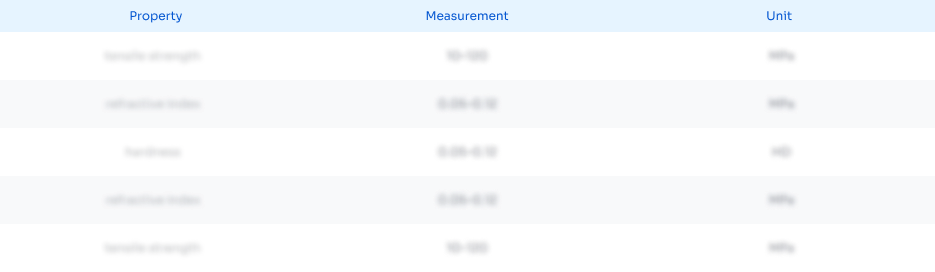
Abstract
Description
Claims
Application Information

- Generate Ideas
- Intellectual Property
- Life Sciences
- Materials
- Tech Scout
- Unparalleled Data Quality
- Higher Quality Content
- 60% Fewer Hallucinations
Browse by: Latest US Patents, China's latest patents, Technical Efficacy Thesaurus, Application Domain, Technology Topic, Popular Technical Reports.
© 2025 PatSnap. All rights reserved.Legal|Privacy policy|Modern Slavery Act Transparency Statement|Sitemap|About US| Contact US: help@patsnap.com