Damage repairing method for single-closed-cavity foam sandwich structure
A sandwich structure and foam technology, which is applied in the field of composite blade repair, can solve the problems of exceeding the foam compression bearing capacity, prone to skin steps, and insufficient foam compression strength, so as to solve skin collapse and avoid blade overweight Effect
- Summary
- Abstract
- Description
- Claims
- Application Information
AI Technical Summary
Problems solved by technology
Method used
Image
Examples
Embodiment Construction
[0031] Attached below Figure 1-3 The application is described in further detail with the specific embodiment:
[0032] The application belongs to the field of repair methods for main and tail rotor blade skin debonding and internal foam damage of rotor system composite materials. Specifically, the composite blade repair technology relates to a repair method for composite blade skin and internal foam filling after damage.
[0033] In relative technology, glue injection repair is generally considered for small debonding areas, but traditional glue injection repairs generally use glue injection guns, and the pressure of glue injection is uncontrollable, which can easily cause the debonding area to expand; in addition, due to the lack of system The analysis and data support lead to problems such as overweight of the blade after glue injection.
[0034] This application improves the relative technical scheme, analyzes in detail the relationship between the debonding area and the...
PUM
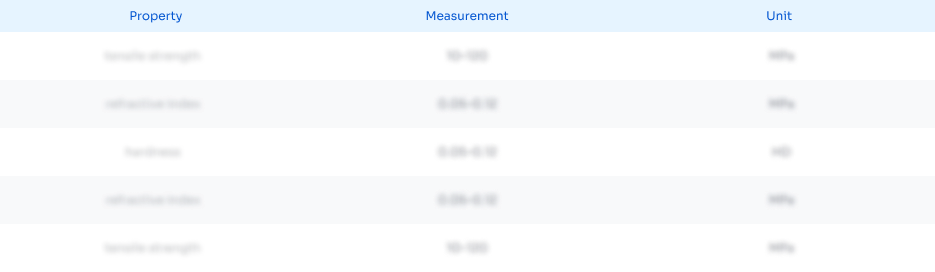
Abstract
Description
Claims
Application Information

- Generate Ideas
- Intellectual Property
- Life Sciences
- Materials
- Tech Scout
- Unparalleled Data Quality
- Higher Quality Content
- 60% Fewer Hallucinations
Browse by: Latest US Patents, China's latest patents, Technical Efficacy Thesaurus, Application Domain, Technology Topic, Popular Technical Reports.
© 2025 PatSnap. All rights reserved.Legal|Privacy policy|Modern Slavery Act Transparency Statement|Sitemap|About US| Contact US: help@patsnap.com