Concrete building block and preparation method thereof
A technology for adding blocks and concrete, applied in the field of adding concrete blocks and their preparation, can solve problems such as unfavorable handling, heavy workload, unfavorable contact surface maintenance, etc., and achieve the effects of avoiding overweight, high product strength, and easy loading, unloading and handling.
- Summary
- Abstract
- Description
- Claims
- Application Information
AI Technical Summary
Problems solved by technology
Method used
Image
Examples
Embodiment 1
[0037] A concrete block is prepared from the following raw materials in parts by weight: 900 parts of iron ore tailings, 600 parts of fly ash, 250 parts of lime, 120 parts of cement and 1.95 parts of aluminum powder.
[0038] The preparation method of described concrete plus block, comprises the following steps:
[0039] (1) The iron ore tailings are ball-milled to pulp, and after the ball-milling is completed, the mixed fly ash is prepared into a mortar with a specific gravity of 1.6kg / L;
[0040] (2) Lime, cement and aluminum powder are added to the mortar in step (1) and stirred, and the stirring is carried out for 150s to obtain the mixture; at this time, the mixture is dispersed mutually to make the uniformity of the slurry better, and the stirring result is right Product quality has a certain influence;
[0041] (3) pouring the mixture of step (3) into a mold for molding, the temperature during pouring is controlled at 39°C, and 2.5 hours of constant temperature and sta...
Embodiment 2
[0045] A concrete block is prepared from the following raw materials in parts by weight: 950 parts of iron ore tailings, 650 parts of fly ash, 240 parts of lime, 80 parts of cement and 1.8 parts of aluminum powder.
[0046] The preparation method of described concrete plus block, comprises the following steps:
[0047] (1) The iron ore tailings are ball-milled to pulp, and after the ball-milling is completed, the mixed fly ash is prepared into a mortar with a specific gravity of 1.6kg / L;
[0048](2) Lime, cement and aluminum powder are added to the mortar in step (1) and stirred, and the stirring is carried out for 150s to obtain the mixture; at this time, the mixture is dispersed mutually to make the uniformity of the slurry better, and the stirring result is right Product quality has a certain influence;
[0049] (3) pour the mixture of step (3) into a mold for molding, the temperature during pouring is controlled at 37°C, and a constant temperature and static curing of 55°...
Embodiment 3
[0053] A concrete block is prepared from the following raw materials in parts by weight: 1000 parts of iron ore tailings, 700 parts of fly ash, 280 parts of lime, 100 parts of cement and 1.9 parts of aluminum powder.
[0054] The preparation method of described concrete plus block, comprises the following steps:
[0055] (1) The iron ore tailings are ball-milled to pulp, and after the ball-milling is completed, the mixed fly ash is prepared into a mortar with a specific gravity of 1.6kg / L;
[0056] (2) Lime, cement and aluminum powder are added to the mortar in step (1) and stirred, and the stirring is carried out for 150s to obtain the mixture; at this time, the mixture is dispersed mutually to make the uniformity of the slurry better, and the stirring result is right Product quality has a certain influence;
[0057] (3) pouring the mixture of step (3) into a mold for molding, the temperature during pouring is controlled at 36°C, and a constant temperature static curing of 5...
PUM
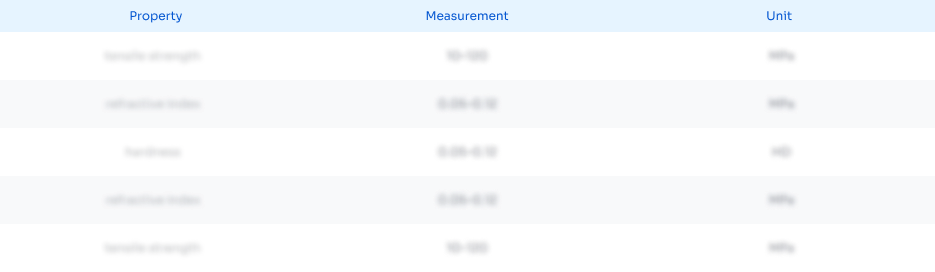
Abstract
Description
Claims
Application Information

- R&D Engineer
- R&D Manager
- IP Professional
- Industry Leading Data Capabilities
- Powerful AI technology
- Patent DNA Extraction
Browse by: Latest US Patents, China's latest patents, Technical Efficacy Thesaurus, Application Domain, Technology Topic, Popular Technical Reports.
© 2024 PatSnap. All rights reserved.Legal|Privacy policy|Modern Slavery Act Transparency Statement|Sitemap|About US| Contact US: help@patsnap.com