Particle-reinforced fiber-woven composite material and preparation method thereof
A technology of fiber braiding and particle reinforcement, which is applied in the field of particle-reinforced fiber braided composite materials and its preparation, can solve the problems of fiber damage, cumbersome preparation process, and increased manufacturing cost, and achieve improved density, simplified preparation steps, and reduced The effect of stomatal defects
- Summary
- Abstract
- Description
- Claims
- Application Information
AI Technical Summary
Problems solved by technology
Method used
Image
Examples
Embodiment 1
[0032] 1) With spherical ZrO 2 Particles are solid phase, polyvinyl alcohol is used as dispersant, and impregnated ZrO 2 Slurry, wherein the solid phase volume content is 40%;
[0033] 2) Lay the SiC fiber cloth on the graphite mold, using the ZrO2 configured in 1) 2 The slurry is evenly coated on the surface of the SiC fiber cloth, and the impregnated particle slurry is smoothed by the scraper method, and the thickness is set to 0.35mm to obtain the impregnated ZrO 2 Slurry SiC fiber cloth;
[0034] 3) In impregnated ZrO 2 Place another piece of SiC fiber cloth on the SiC fiber cloth of the slurry, and then perform ZrO 2 Slurry coating, squeegeeing, thickness setting, repeating the process of lamination and particle slurry impregnation to make ZrO-containing 2 SiC fiber stack of particles; the ZrO-containing 2 The granular SiC fiber stack was embedded in a water-absorbent resin, placed in a mold, and slowly applied a pressure of 30 MPa to the surface of the stack for pr...
Embodiment 2
[0038] 1) With spherical ZrO 2 Particles are solid phase, polyvinyl alcohol is used as dispersant, and impregnated ZrO 2 Slurry, wherein the solid phase volume content is 50%;
[0039] 2) Lay the SiC fiber cloth on the graphite mold, using the ZrO2 configured in 1) 2 The slurry is evenly coated on the surface of the SiC fiber cloth, and the impregnated particle slurry is smoothed by the scraper method, and the thickness is set to 0.4mm to obtain the impregnated ZrO 2 Slurry SiC fiber cloth;
[0040] 3) In impregnated ZrO 2 Place another piece of SiC fiber cloth on the SiC fiber cloth of the slurry, and then perform ZrO 2 Slurry coating, squeegeeing, thickness setting, repeating the process of lamination and particle slurry impregnation to make ZrO-containing 2 SiC fiber stack of particles; the ZrO-containing 2 The granular SiC fiber stack was embedded in a water-absorbing resin, placed in a mold, and a pressure of 35 MPa was slowly applied to the surface of the stack for...
Embodiment 3
[0044] 1) Using spherical SiC particles as the solid phase and polyvinyl alcohol as the dispersant, prepare impregnated SiC slurry, wherein the volume content of the solid phase is 50%;
[0045] 2) Spread the C fiber cloth on the mold, use the SiC slurry configured in 1) to evenly coat the surface of the C fiber cloth, use the scraper method to smooth the impregnated particle slurry, and set the thickness to 0.35mm to obtain the impregnated SiC Slurry C fiber cloth;
[0046] 3) Place another piece of C fiber cloth on the C fiber cloth impregnated with SiC slurry, then apply SiC slurry, squeegee, set the thickness, repeat the process of lamination and particle slurry impregnation, and make SiC particles C fiber stacking body; the C fiber stacking body containing SiC particles is embedded in a water-absorbent resin, placed in a mold, and a pressure of 35 MPa is slowly applied to the surface of the stacking body for pressing, and the pressure is maintained for 15 minutes; the mol...
PUM
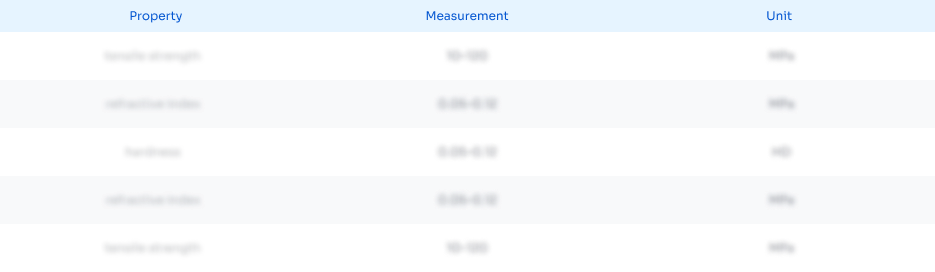
Abstract
Description
Claims
Application Information

- R&D
- Intellectual Property
- Life Sciences
- Materials
- Tech Scout
- Unparalleled Data Quality
- Higher Quality Content
- 60% Fewer Hallucinations
Browse by: Latest US Patents, China's latest patents, Technical Efficacy Thesaurus, Application Domain, Technology Topic, Popular Technical Reports.
© 2025 PatSnap. All rights reserved.Legal|Privacy policy|Modern Slavery Act Transparency Statement|Sitemap|About US| Contact US: help@patsnap.com