Full scrap steel electric furnace steelmaking continuous feeding system and method
An electric furnace steelmaking and feeding system technology, which is applied in the field of steelmaking, can solve the problems of rough feeding volume, low feeding speed control accuracy, and low overall efficiency, and achieve the effects of reducing manpower use, improving feeding efficiency, and uniform feeding
- Summary
- Abstract
- Description
- Claims
- Application Information
AI Technical Summary
Problems solved by technology
Method used
Image
Examples
Embodiment 1
[0017] Such as figure 1 , a continuous feeding system for all-scrap electric furnace steelmaking, including a plurality of storage bins and a conveying mechanism, the storage bins are used to store scrap steel, the conveying mechanism is used to transport scrap steel to the electric furnace for continuous feeding, and the conveying mechanism includes a horizontal conveyor belt 1 and Feeding conveyor belt 2, a plurality of storage bins are arranged along the conveying direction of the horizontal conveyor belt, in this embodiment, there are 5, the feeding conveyor belt 2 is connected between the storage bin and the horizontal conveyor belt, and the horizontal conveyor belt 1 is connected to the electric furnace , at least one storage bin along the near end of the electric furnace is a light and thin bin 3. In this embodiment, there are two thin and light bins, and the remaining storage bins are heavy bins 4; the feeding conveyor belt and the horizontal conveyor belt can use chain...
Embodiment 3
[0024] The entrainment of light and thin materials is relatively large. Reducing the amount of light and thin materials is conducive to improving the quality of steelmaking. Therefore, it is hoped to increase the amount of heavy materials. Specifically, in this plan, a larger secondary reference value is set. Since the quality, shape, and size of scrap steel vary greatly with the batch of incoming materials, it also has a great influence on the fluctuation range of feeding. The greater the difference in the shape and size of scrap steel, the greater the fluctuation caused, and when the fluctuation range is large. If the secondary reference value is set too large, the fluctuation range may exceed the total feeding speed, and subsequent light and thin material compensation will fail. To solve this problem, in this embodiment, when formulating the secondary reference value, first calculate the standard deviation σ of the primary weighing measurement value and the secondary weighin...
PUM
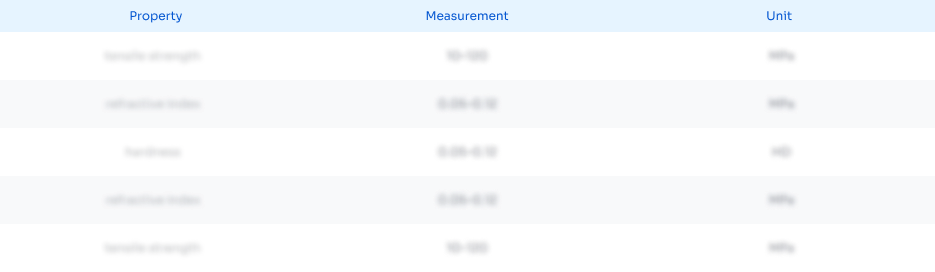
Abstract
Description
Claims
Application Information

- R&D
- Intellectual Property
- Life Sciences
- Materials
- Tech Scout
- Unparalleled Data Quality
- Higher Quality Content
- 60% Fewer Hallucinations
Browse by: Latest US Patents, China's latest patents, Technical Efficacy Thesaurus, Application Domain, Technology Topic, Popular Technical Reports.
© 2025 PatSnap. All rights reserved.Legal|Privacy policy|Modern Slavery Act Transparency Statement|Sitemap|About US| Contact US: help@patsnap.com