A kind of aluminum alloy for extrusion and preparation method thereof
A technology of aluminum alloy and master alloy, which is applied in the direction of manufacturing tools, heat treatment equipment, furnaces, etc., can solve problems such as poor fluidity and ductility, poor toughness of aluminum alloy materials, and poor organizational continuity, so as to eliminate the interference of impurities and realize Corrosion resistance, effect of improving extrusion fluidity
- Summary
- Abstract
- Description
- Claims
- Application Information
AI Technical Summary
Problems solved by technology
Method used
Image
Examples
Embodiment 1
[0034] The components of the aluminum alloy for extrusion and the mass percentage of each component are: Si 0.18%, Fe 0.23%, Mn 2.23%, Zn 0.14%, Er 0.05%, Ti 0.02%, Be 0.06%, V 0.015%, The rest are Al and unavoidable impurities, and the total amount of impurities does not exceed 0.015%.
[0035] The preparation method of aluminum alloy for extrusion comprises the following steps:
[0036] S1: Put the Al99.70 remelted aluminum ingot into the smelting furnace, heat and melt, keep at 795℃, add a refining agent to the solution, and use high-purity nitrogen with a purity of ≥99.999% for a refining, refining time 45min, static After 45 minutes, the molten aluminum was put into the holding furnace.
[0037] S2: Alloy the molten aluminum in a holding furnace, set the temperature to 795°C, add aluminum-iron alloy, aluminum-manganese alloy, aluminum-zinc alloy, aluminum-erbium alloy, aluminum-titanium alloy, aluminum-beryllium alloy, aluminum-vanadium alloy, and use electromagnetic St...
Embodiment 2
[0044] The composition of the aluminum alloy for extrusion and the mass percentage of each composition are: Si 0.1%, Fe 0.16%, Mn 1.8%, Zn 0.18%, Er 0.06%, Ti 0.015%, Be 0.08%, V 0.02%, the rest For Al and unavoidable impurities, the total amount of impurities does not exceed 0.015%.
[0045] The preparation method of aluminum alloy for extrusion comprises the following steps:
[0046] S1: Put the remelted aluminum ingot of Al99.70 into the smelting furnace, heat and melt it, keep it at 780℃, add a refining agent to the solution, and use high-purity nitrogen with a purity of ≥99.999% for a refining, refining time 40min, static After 45 minutes, the molten aluminum was put into the holding furnace.
[0047] S2: Alloy the liquid aluminum in a holding furnace, set the temperature to 780°C, add aluminum-iron alloy, aluminum-manganese alloy, aluminum-zinc alloy, aluminum-erbium alloy, aluminum-titanium alloy, aluminum-beryllium alloy, aluminum-vanadium alloy, use electromagnetic ...
Embodiment 3
[0054] The components of the aluminum alloy for extrusion and the mass percentage of each component are: Si 0.2%, Fe 0.2%, Mn 2%, Zn 0.05%, Er 0.03%, Ti 0.04%, Be 0.04%, V 0.01%, The rest are Al and unavoidable impurities, and the total amount of impurities does not exceed 0.015%.
[0055] The preparation method of aluminum alloy for extrusion comprises the following steps:
[0056] S1: Put the remelted aluminum ingot of Al99.70 into the smelting furnace, heat and melt it, keep it at 800 °C, add a refining agent to the solution, and use high-purity nitrogen with a purity of ≥99.999% for a refining, refining time 40min, static After 45 minutes, the molten aluminum was put into the holding furnace.
[0057] S2: Alloy the liquid aluminum in a holding furnace, set the temperature to 800 °C, add aluminum-iron alloy, aluminum-manganese alloy, aluminum-zinc alloy, aluminum-erbium alloy, aluminum-titanium alloy, aluminum-beryllium alloy, aluminum-vanadium alloy, and use electromagnet...
PUM
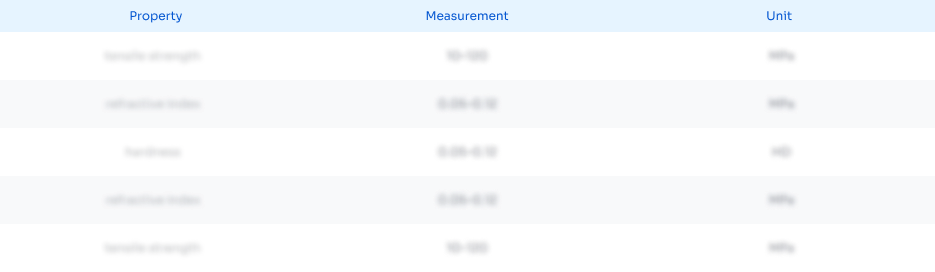
Abstract
Description
Claims
Application Information

- R&D
- Intellectual Property
- Life Sciences
- Materials
- Tech Scout
- Unparalleled Data Quality
- Higher Quality Content
- 60% Fewer Hallucinations
Browse by: Latest US Patents, China's latest patents, Technical Efficacy Thesaurus, Application Domain, Technology Topic, Popular Technical Reports.
© 2025 PatSnap. All rights reserved.Legal|Privacy policy|Modern Slavery Act Transparency Statement|Sitemap|About US| Contact US: help@patsnap.com