Integrated forming method for composite material cabin section
A technology of composite materials and molding methods, which is applied in the field of integrated molding of composite material compartments, can solve the problems of multiple mold modules, difficult operation, waste of raw materials, etc., and achieve the effect of ensuring accuracy and continuity
- Summary
- Abstract
- Description
- Claims
- Application Information
AI Technical Summary
Problems solved by technology
Method used
Image
Examples
Embodiment 1
[0063] In this embodiment, a composite cabin section is a skin panel structure, and its section is a special-shaped section. The interior of the cabin section includes characteristic structures such as bosses, ribs, flanges, and end frames, and the outer surface includes windows, edges, etc. side structures.
[0064] The prepreg in this embodiment is a prepreg obtained by impregnating a carbon fiber prefabricated body with an epoxy resin system glue, and the thickness of a single layer is 0.3 mm. The soft mold uses uncured rubber and glass fiber epoxy resin system prepreg.
[0065] The specific implementation steps of this embodiment are as follows:
[0066] (1) Apply mold release wax on the cleaned mold surface, then install the block on the core mold of the corresponding unit, and use pins and screws for positioning and fastening.
[0067] (2) Lay the carbon fiber prepregs that have been laid down on the surface of the corresponding unit male mold respectively. The first l...
PUM
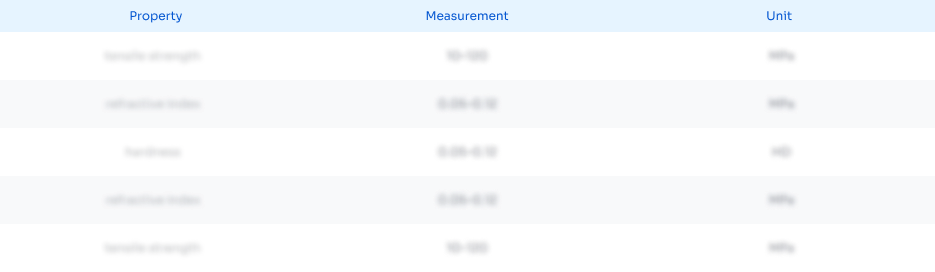
Abstract
Description
Claims
Application Information

- R&D
- Intellectual Property
- Life Sciences
- Materials
- Tech Scout
- Unparalleled Data Quality
- Higher Quality Content
- 60% Fewer Hallucinations
Browse by: Latest US Patents, China's latest patents, Technical Efficacy Thesaurus, Application Domain, Technology Topic, Popular Technical Reports.
© 2025 PatSnap. All rights reserved.Legal|Privacy policy|Modern Slavery Act Transparency Statement|Sitemap|About US| Contact US: help@patsnap.com