Preparation method of ultrahigh-strength aluminum alloy with high creep resistance
A creep performance, aluminum alloy technology, applied in the field of ultra-high strength aluminum alloy preparation with high creep resistance, can solve problems such as poor creep resistance, achieve no coarse grain boundary phase, expand application prospects, room temperature and high temperature The effect of improved creep resistance
- Summary
- Abstract
- Description
- Claims
- Application Information
AI Technical Summary
Problems solved by technology
Method used
Image
Examples
preparation example Construction
[0031] The preparation method of the high-strength aluminum alloy of the present application comprises the following steps:
[0032] Step (1), the Zn content is 10.0~13.0wt% by composition weight percentage, the Mg content is 1.9~3.2wt%, the Cu content is 1.2~2.2wt%, the Ti content is 0.02~0.2wt%, the Zr content is 0.10-0.20wt%, Sc content is 0.1-0.2wt%, impurity element Si content≤0.05wt%, Fe content≤0.05wt%, and Fe>Si, and the rest are Al raw materials for master alloy fusion. Alloy melting is carried out in a resistance furnace using a graphite crucible. When the temperature of the graphite crucible reaches 200°C±5°C, add preheated raw materials, and the melting temperature is controlled at 760°C±5°C. After the alloy is completely melted, keep it warm for 18- For 22 minutes, cool down to 740°C±5°C for melt treatment, stir, refine and degas and remove slag, then let stand for 8-12 minutes, cool down to 720°C±5°C, cast into metal molds, and cut into pieces after solidificatio...
Embodiment 1
[0038] Al-11Zn-2.45Mg-1.7Cu-0.17Zr-0.2Sc alloy was spray deposited.
[0039] The percentage by weight of the components is that the Zn content is 11wt%, the Mg content is 2.45wt%, the Cu content is 1.7wt%, the Ti content is 0.1wt%, the Zr content is 0.17wt%, the Sc content is 0.2wt%, and the impurity element Si The content of Fe is 0.025wt%, the content of Fe is 0.045wt%, and the rest is Al for master alloy fusion.
[0040] Alloy melting is carried out in a resistance furnace using a graphite crucible. When the temperature of the graphite crucible reaches 200°C, add preheated raw materials. The melting temperature is controlled at 760°C. After the alloy is completely melted, it is kept for 20 minutes and then cooled to 740°C. Melt treatment, stirring, refining, degassing and slag removal, let stand for 10 minutes, cool down to 720°C, cast into metal molds, and cut into Small ingots, as master alloy materials for spray forming.
[0041] Under the condition of inert gas prote...
Embodiment 2
[0051] Al-11Zn-2.45Mg-1.7Cu-0.17Zr-0.3Sc alloy was spray deposited.
[0052] The percentage by weight of the components is that the Zn content is 11wt%, the Mg content is 2.45wt%, the Cu content is 1.7wt%, the Ti content is 0.1wt%, the Zr content is 0.17wt%, the Sc content is 0.3wt%, and the impurity element Si The content of Fe is 0.025wt%, the content of Fe is 0.045wt%, and the rest is Al for master alloy fusion.
[0053] Alloy melting is carried out in a resistance furnace using a graphite crucible. When the temperature of the graphite crucible reaches 200°C, add preheated raw materials. The melting temperature is controlled at 760°C. After the alloy is completely melted, it is kept for 20 minutes and then cooled to 740°C. Melt treatment, stirring, refining, degassing and slag removal, let stand for 10 minutes, cool down to 720°C, cast into metal molds, and cut into Small ingots, as master alloy materials for spray forming.
[0054] Under the condition of inert gas prote...
PUM
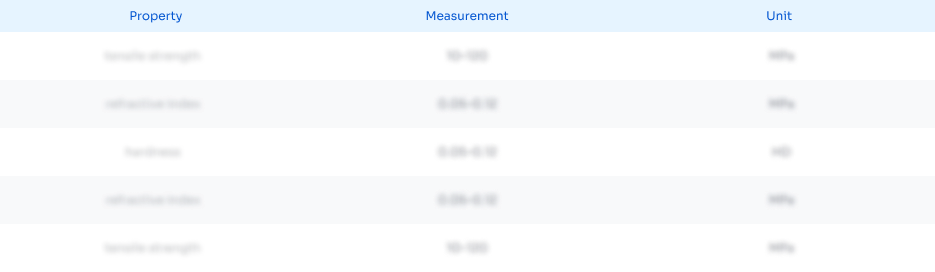
Abstract
Description
Claims
Application Information

- R&D
- Intellectual Property
- Life Sciences
- Materials
- Tech Scout
- Unparalleled Data Quality
- Higher Quality Content
- 60% Fewer Hallucinations
Browse by: Latest US Patents, China's latest patents, Technical Efficacy Thesaurus, Application Domain, Technology Topic, Popular Technical Reports.
© 2025 PatSnap. All rights reserved.Legal|Privacy policy|Modern Slavery Act Transparency Statement|Sitemap|About US| Contact US: help@patsnap.com