CeO2/MnO2 composite photocatalyst as well as preparation method and application thereof
A catalyst and composite light technology, applied in metal/metal oxide/metal hydroxide catalysts, physical/chemical process catalysts, chemical instruments and methods, etc., to improve photocatalytic performance, prolong life, and improve the utilization rate of visible light. Effect
- Summary
- Abstract
- Description
- Claims
- Application Information
AI Technical Summary
Problems solved by technology
Method used
Image
Examples
Embodiment 1
[0032] (1)MnO 2 Preparation of nanorods
[0033] 2.48g manganese sulfate hydrate (MnSO 4 ·H 2 O), 1.66g potassium permanganate (KMnO 4 ) was placed in a 150mL stainless steel autoclave with a polytetrafluoroethylene liner, 75mL of ultrapure water was added, and the constant temperature heat reaction was maintained at 160°C for 4h; after the reaction was completed, it was naturally cooled to room temperature, and centrifuged and washed 3 times with ultrapure water, and the obtained The sample was dried at a constant temperature of 110°C for 12 hours; the dried sample was placed in a muffle furnace and calcined at 300°C for 6 hours. After the calcination was completed and the product was lowered to room temperature, the product was taken out and ground to obtain MnO 2 Nanorods, save for future use.
[0034] (2) Preparation of CeO with a loading capacity of 5% 2 / MnO 2 composite material
[0035] At room temperature, 0.5 g of MnO 2 Slowly add the rod into the mixed solution...
Embodiment 2
[0037] (1)MnO 2 Preparation of nanorods
[0038] 2.48g manganese sulfate hydrate (MnSO 4 ·H 2 O), 1.66g potassium permanganate (KMnO 4 ) was placed in a 150mL stainless steel autoclave with a polytetrafluoroethylene liner, 75mL of ultrapure water was added, and the constant temperature heat reaction was maintained at 160°C for 4h; after the reaction was completed, it was naturally cooled to room temperature, and centrifuged and washed 3 times with ultrapure water, and the obtained The sample was dried at a constant temperature of 110°C for 12 hours; the dried sample was placed in a muffle furnace and calcined at 300°C for 6 hours. After the calcination was completed and the product was lowered to room temperature, the product was taken out and ground to obtain MnO 2 Nanorods, save for future use.
[0039] (2) Preparation of CeO with a loading capacity of 10% 2 / MnO 2 composite material
[0040] At room temperature, 0.5 g of MnO 2 Slowly add the rod into the mixed solut...
Embodiment 3
[0042] (1)MnO 2 Preparation of nanorods
[0043] 2.48g manganese sulfate hydrate (MnsO 4 ·H 2 O), 1.66g potassium permanganate (KMnO 4 ) was placed in a 150mL stainless steel autoclave with a polytetrafluoroethylene liner, 75mL of ultrapure water was added, and the constant temperature heat reaction was maintained at 160°C for 4h; after the reaction was completed, it was naturally cooled to room temperature, and centrifuged and washed 3 times with ultrapure water, and the obtained The sample was dried at a constant temperature of 110°C for 12 hours; the dried sample was placed in a muffle furnace and calcined at 300°C for 6 hours. After the calcination was completed and the product was lowered to room temperature, the product was taken out and ground to obtain MnO 2 Nanorods, save for future use.
[0044] (2) Preparation of CeO with a loading capacity of 30% 2 / MnO 2 composite material
[0045] At room temperature, 0.5 g of MnO 2 Slowly add the rod into the mixed solut...
PUM
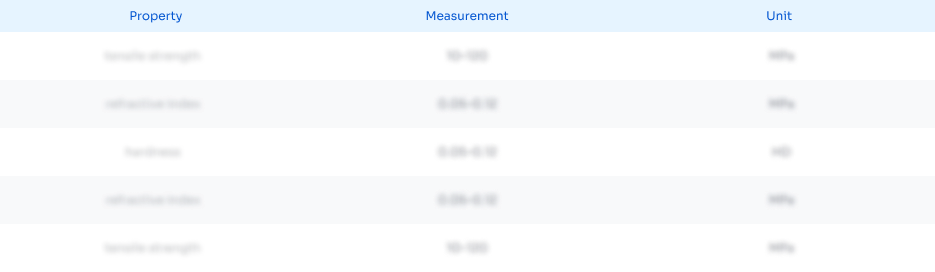
Abstract
Description
Claims
Application Information

- R&D
- Intellectual Property
- Life Sciences
- Materials
- Tech Scout
- Unparalleled Data Quality
- Higher Quality Content
- 60% Fewer Hallucinations
Browse by: Latest US Patents, China's latest patents, Technical Efficacy Thesaurus, Application Domain, Technology Topic, Popular Technical Reports.
© 2025 PatSnap. All rights reserved.Legal|Privacy policy|Modern Slavery Act Transparency Statement|Sitemap|About US| Contact US: help@patsnap.com