Preparation method and application of carbon fiber/silicon carbide oriented porous skeleton
A porous skeleton and carbon fiber technology, applied in the field of phase change heat storage, can solve the problems of slow heat storage and release speed, leakage heat storage and release speed, and high technical difficulty of phase change materials, and achieve excellent thermal response speed and anti-leakage ability. The method is simple and the process cost is low
- Summary
- Abstract
- Description
- Claims
- Application Information
AI Technical Summary
Problems solved by technology
Method used
Image
Examples
Embodiment 1
[0028] 1. Preparation of carbon fiber / silicon carbide porous framework
[0029] (1) Slurry preparation: Weigh 6g of silicon dioxide powder with a particle size of 500nm and 3.085g of silicon powder (the molar ratio of silicon to silicon dioxide is 1.1), uniformly mix, dry and grind for later use. A CMC aqueous solution with a concentration of 1 wt% was prepared (0.101 g of CMC binder and 10 g of deionized water). Take 1.147g of the above-mentioned mixed powder and 0.636g of carbon fiber powder with a particle size of 13 μm, add them to the above-mentioned binder solution and stir and mix (wherein the silicon source and carbon fiber powder account for 15wt% of the slurry, and the molar ratio of carbon to silicon 2), after removing air bubbles, the slurry preparation is completed.
[0030] (2) Freezing and freeze-drying: pour the slurry into a special mold, remove air bubbles, and put the mold into a freezer at -20°C for 15 minutes for pre-freezing. Then put it in a cold trap ...
Embodiment 2
[0036] 1. Preparation of Carbon Fiber / Silicon Carbide Skeleton Structure
[0037] (1) Slurry preparation: Weigh 6g of silicon dioxide powder with a particle size of 500nm and 5.61g of silicon powder (the molar ratio of silicon to silicon dioxide is 2), uniformly mix, dry and grind for later use. Prepare a CMC solution with a concentration of 1.5wt% (the quality of the CMC binder is 0.152g, and the quality of deionized water is 10g), take 1.106g of the above-mentioned mixed powder and 0.685g of carbon fiber powder with a particle size of 13 μm, and add them to the above-mentioned adhesive Stir and mix in the binder solution (the silicon source and carbon fiber powder account for 15 wt% of the slurry, and the molar ratio of carbon to silicon is 2), and after removing air bubbles, the slurry preparation is completed.
[0038] (2) Freezing and freeze-drying: the slurry is poured into a special mold, and after removing air bubbles, the mold is placed in a -20°C freezer for pre-free...
Embodiment 3
[0043] (1) Slurry preparation: Weigh 6g of silicon dioxide powder with a particle size of 500nm and 2.806g of silicon powder (the molar ratio of silicon to silicon dioxide is 1), uniformly mix, dry and grind for later use. Prepare a CMC solution with a concentration of 0.5wt% (the quality of the CMC binder is 0.051g, and the quality of deionized water is 10g), take 1.394g of the above-mentioned mixed powder and 0.380g of carbon fiber powder with a particle size of 13 μm, and add them to the above-mentioned adhesive Stir and mix in the binder solution (the silicon source and the carbon fiber powder account for 15 wt% of the slurry, and the molar ratio of carbon to silicon is 1), and the slurry preparation is completed after removing air bubbles.
[0044] (2) Freezing and freeze-drying: pour the slurry into a special mold, remove air bubbles, and put the mold into a freezer at -20°C for 15 minutes for pre-freezing. Then the pre-frozen samples were placed in a cold trap at -65 °C...
PUM
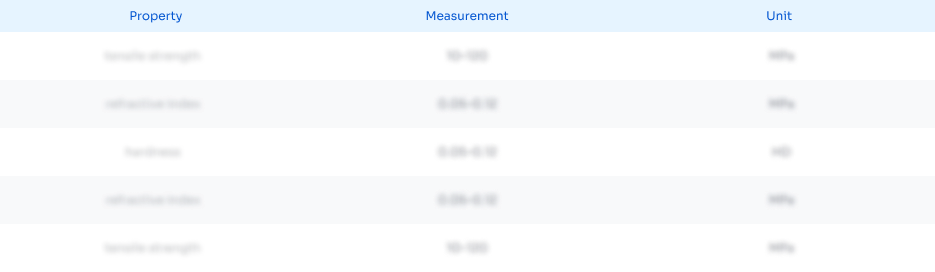
Abstract
Description
Claims
Application Information

- R&D Engineer
- R&D Manager
- IP Professional
- Industry Leading Data Capabilities
- Powerful AI technology
- Patent DNA Extraction
Browse by: Latest US Patents, China's latest patents, Technical Efficacy Thesaurus, Application Domain, Technology Topic, Popular Technical Reports.
© 2024 PatSnap. All rights reserved.Legal|Privacy policy|Modern Slavery Act Transparency Statement|Sitemap|About US| Contact US: help@patsnap.com