Automatic feeding process for constant melting speed electroslag furnace
A technology of electroslag furnace and melting rate, which is applied in the field of automatic feeding process of electroslag furnace with constant melting rate, can solve the problems of difference in quality level, unstable feeding quality of the riser end of electroslag ingot, etc.
- Summary
- Abstract
- Description
- Claims
- Application Information
AI Technical Summary
Problems solved by technology
Method used
Examples
Embodiment 1
[0015] Example 1: An automatic feeding process for constant melting rate electroslag furnace, using 42CrMoA steel, ingot size: 7.6 tons, crystallizer: Φ790 / 830mm, quantity: 3 pieces, slag system: CaF 2 :Al 2 o 3 :CaO=65:30:5, slag amount: 300kg, consumable electrode specification is Φ600mm die casting slab, and the set melting rate in the normal stage of electroslag remelting is 9.5kg / min.
[0016] According to t =7~10v, the theoretical total time of electroslag remelting feeding stage is theoretically calculated to be 67~95min.
[0017] When the real-time melting rate drops to (0.80~0.70) times the set melting rate for remelting, the theoretically calculated range of melting rate at the beginning of the second feeding stage is 7.6~6.6kg / min, and the melting rate at the beginning of the fourth feeding stage The range of melting rate is 3.8~2.8kg / min. Set the melting rate at the beginning of the second feeding stage to 7kg / min, and set the melting rate at the beginning of th...
PUM
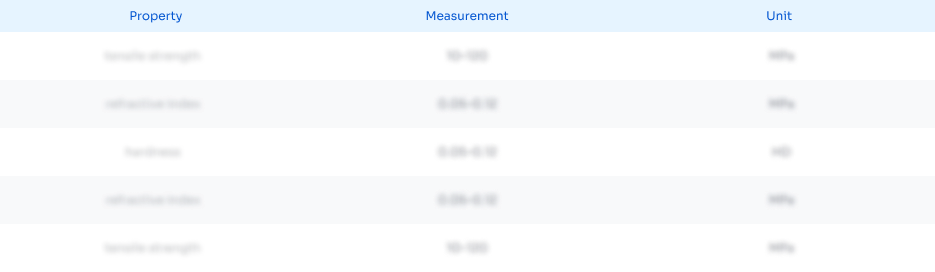
Abstract
Description
Claims
Application Information

- R&D
- Intellectual Property
- Life Sciences
- Materials
- Tech Scout
- Unparalleled Data Quality
- Higher Quality Content
- 60% Fewer Hallucinations
Browse by: Latest US Patents, China's latest patents, Technical Efficacy Thesaurus, Application Domain, Technology Topic, Popular Technical Reports.
© 2025 PatSnap. All rights reserved.Legal|Privacy policy|Modern Slavery Act Transparency Statement|Sitemap|About US| Contact US: help@patsnap.com