Production method of plastic die steel ZW636
A ZW636, plastic mold steel technology, applied in the direction of improving process efficiency and manufacturing converters, can solve the problems of reducing production costs, large temperature drop of molten steel, low purity of molten steel, etc., to reduce production costs and overcome temperature drop of molten steel big effect
- Summary
- Abstract
- Description
- Claims
- Application Information
AI Technical Summary
Problems solved by technology
Method used
Examples
Embodiment 1
[0115] The present embodiment provides a kind of production method of described plastic mold steel ZW636, and described production method comprises the following steps:
[0116] (1) Carry out vanadium-containing molten iron blowing for 5.5 minutes, add vanadium-extracting materials at 1380°C, and the oxygen supply intensity of the converter is 2.2m 3 / t·min, keep the final temperature of vanadium extraction and blowing at 1380°C, in which vanadium extraction materials include 25kg / t and iron oxide scale 13kg / t;
[0117] Desulfurization agent after vanadium extraction and blowing, wherein the desulfurization agent includes 9kg / t lime powder, 1.3kg / t fluorite powder and 0.8kg / t aluminum powder, desulfurize for 13min under the first stirring at a rotation speed of 83r / min, Obtaining a desulfurized semi-steel with a sulfur content of 0.01wt%;
[0118] (2) Mixing the desulfurized rear semi-steel and nickel-containing pig iron described in step (1), wherein the addition of nickel-c...
Embodiment 2
[0125] The present embodiment provides a kind of production method of described plastic mold steel ZW636, and described production method comprises the following steps:
[0126] (1) Carry out vanadium-containing molten iron blowing for 5 minutes, add vanadium-extracting materials at 1360°C, and the oxygen supply intensity of the converter is 2.3m 3 / t·min, keep the final temperature of vanadium extraction blowing at 1360℃, in which vanadium extraction materials include 20kg / t and iron oxide scale 15kg / t;
[0127] Desulfurization agent after vanadium extraction and blowing, wherein the desulfurization agent includes 8kg / t of lime powder, 1.5kg / t of fluorite powder and 1kg / t of aluminum powder, and desulfurizes for 15min under the first stirring with a rotation speed of 80r / min to obtain Desulfurized semi-steel with sulfur content ≤0.01wt%;
[0128] (2) Mixing step (1) described desulfurization rear semi-steel and nickel-containing pig iron, wherein the add-on of nickel-contain...
Embodiment 3
[0135] The present embodiment provides a kind of production method of described plastic mold steel ZW636, and described production method comprises the following steps:
[0136] (1) Carry out vanadium-containing molten iron blowing for 6 minutes, add vanadium-extracting materials at 1400°C, and the oxygen supply intensity of the converter is 2m 3 / t·min, keep the final temperature of vanadium extraction blowing at 1400℃, in which vanadium extraction materials include 30kg / t and iron oxide scale 10kg / t;
[0137] Desulfurization agent after vanadium extraction and blowing, wherein the desulfurization agent includes 10kg / t of lime powder, 1kg / t of fluorite powder and 0.5g / t of aluminum powder, and desulfurizes for 12min under the first stirring at a speed of 85r / min to obtain Desulfurized semi-steel with sulfur content ≤0.01wt%;
[0138] (2) Mixing the semi-steel and nickel-containing pig iron after desulfurization described in step (1), wherein the addition of nickel-containing...
PUM
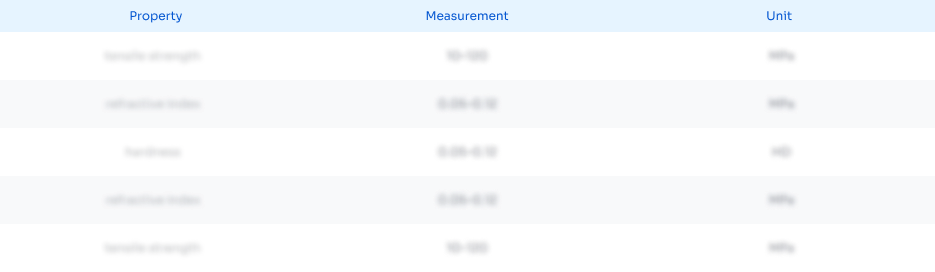
Abstract
Description
Claims
Application Information

- R&D Engineer
- R&D Manager
- IP Professional
- Industry Leading Data Capabilities
- Powerful AI technology
- Patent DNA Extraction
Browse by: Latest US Patents, China's latest patents, Technical Efficacy Thesaurus, Application Domain, Technology Topic, Popular Technical Reports.
© 2024 PatSnap. All rights reserved.Legal|Privacy policy|Modern Slavery Act Transparency Statement|Sitemap|About US| Contact US: help@patsnap.com