Preparation method for forming lithium molybdate diaphragm coating in situ
A technology of lithium molybdate and diaphragm, which is applied in the field of electrochemical energy storage devices, can solve the problems of low utilization rate of active materials, decreased lifespan, and decreased battery capacity, and achieves low utilization rate of active materials, reduced capacity decay rate, and simple The effect of synthetic methods
- Summary
- Abstract
- Description
- Claims
- Application Information
AI Technical Summary
Problems solved by technology
Method used
Examples
preparation example Construction
[0019] A preparation method for forming a lithium molybdate diaphragm coating in situ: it is characterized in that it comprises the steps:
[0020] 1. First add 1-2g (NH 4 ) 6 Mo 7 o 24 4H 2 O dissolved in HNO 3 / H 2 In a beaker of O (1:5, v / v), ultrasonically stir for 30 minutes to make it fully mixed.
[0021] 2. Transfer the above solution into the lining of a polytetrafluoroethylene reactor (100ml) and heat it at 200°C for 2h, and wait for it to cool down.
[0022] 3. The product obtained in the reaction kettle was vacuum filtered and washed with deionized water and ethanol in sequence, and finally dried in a vacuum oven at 60°C for 12 hours to obtain white MoO 3 nanorod material.
[0023] 4. Put MoO 3 , Super P, and PVDF were mixed according to the following mass ratio, thoroughly ground for 30 minutes, then dispersed in 10ml of NMP solvent, and magnetically stirred at room temperature for 12 hours to obtain a mixed slurry.
[0024] MoO 3 :Super P:PVDF=45-50:45...
Embodiment 1
[0029] Example 1: At room temperature, 1.6g (NH 4 ) 6 Mo 7 o 24 4H 2 O dissolved in 90ml HNO 3 / H 2 In a beaker of O (1:5, v / v), ultrasonically stir for 30 minutes to make it fully mixed. The above solution was transferred to a polytetrafluoroethylene reactor lining (100ml) and heated at 200°C for 2h, and then cooled. The product obtained in the reaction kettle was vacuum-filtered and washed 5 times with deionized water and ethanol in sequence, and finally dried in a vacuum oven at 60°C for 12 hours to obtain white MoO 3 nanorod material. At room temperature, the MoO 3: Super P: PVDF=0.2g: 0.25g: 0.05g mass ratio mixed, fully ground for 30min, then dispersed in 10ml of NMP solvent, magnetically stirred for 12h to obtain a mixed slurry. Coat the mixed slurry on the ordinary diaphragm with a coating machine and keep it set at room temperature for 1 hour, then transfer it to a vacuum drying oven to dry for 6 hours, and punch the dried coated diaphragm into a 19mm diamete...
Embodiment 2
[0030] Example two: at room temperature, 1.6g (NH 4 ) 6 Mo 7 o 24 4H 2 O dissolved in 90ml HNO 3 / H 2 In a beaker of O (1:5, v / v), ultrasonically stir for 30 minutes to make it fully mixed. The above solution was transferred to a polytetrafluoroethylene reactor lining (100ml) and heated at 200°C for 2h, and then cooled. The product obtained in the reaction kettle was vacuum-filtered and washed 5 times with deionized water and ethanol in sequence, and finally dried in a vacuum oven at 60°C for 12 hours to obtain white MoO 3 nanorod material. At room temperature, the MoO 3 : Super P: PVDF = 0.25g: 0.2g: 0.05g mass ratio mixed, fully ground for 30min, then dispersed in 10ml of NMP solvent, magnetically stirred for 12h to obtain a mixed slurry. Coat the mixed slurry on the ordinary diaphragm with a coating machine and keep it set at room temperature for 1 hour, then transfer it to a vacuum drying oven to dry for 6 hours, and punch the dried coated diaphragm into a 19mm di...
PUM
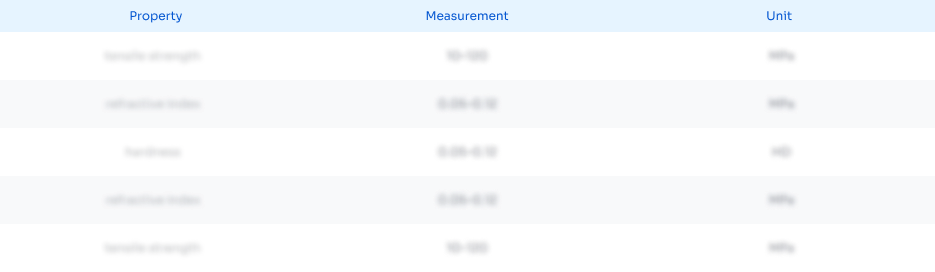
Abstract
Description
Claims
Application Information

- Generate Ideas
- Intellectual Property
- Life Sciences
- Materials
- Tech Scout
- Unparalleled Data Quality
- Higher Quality Content
- 60% Fewer Hallucinations
Browse by: Latest US Patents, China's latest patents, Technical Efficacy Thesaurus, Application Domain, Technology Topic, Popular Technical Reports.
© 2025 PatSnap. All rights reserved.Legal|Privacy policy|Modern Slavery Act Transparency Statement|Sitemap|About US| Contact US: help@patsnap.com