Novel low-phosphorus low-sulfur steel smelting process
A low-sulfur steel and new process technology, applied in the field of iron and steel smelting, can solve the problems of high production cost, low dephosphorization removal rate, unstable control of ultra-low phosphorus and sulfur, etc., and achieve the effect of high matching degree and simple production process
- Summary
- Abstract
- Description
- Claims
- Application Information
AI Technical Summary
Problems solved by technology
Method used
Image
Examples
Embodiment
[0024] In this embodiment, taking the smelting of ER50-6E steel as an example, the new process of smelting low-phosphorus and low-sulfur steel is described in detail, which includes the following steps in turn:
[0025] The chemical composition of this steel grade is as follows:
[0026]
[0027] ER50-6E steel is smelted by a new low-phosphorus and low-sulfur steel smelting process. The specific process steps are as follows:
[0028] S1. Furnace washing and ladle washing before converter smelting;
[0029] S2. Desulfurization of blast furnace molten iron is carried out by KR stirring method. The temperature of molten iron entering the desulfurization station is 1410°C. The dosage of desulfurizer is controlled at 8kg / t. 18 minutes, the sulfur content of the molten iron after desulfurization is 0.0009%, and the high-sulfur slag on the surface of the clean molten iron is removed by blowing argon to remove the slag after desulfurization;
[0030] S3. Use the top-bottom combin...
PUM
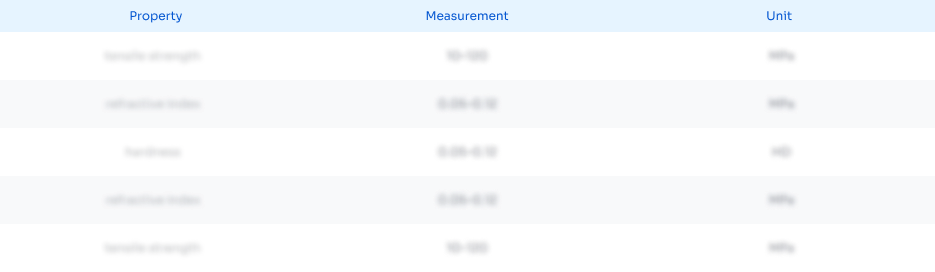
Abstract
Description
Claims
Application Information

- R&D Engineer
- R&D Manager
- IP Professional
- Industry Leading Data Capabilities
- Powerful AI technology
- Patent DNA Extraction
Browse by: Latest US Patents, China's latest patents, Technical Efficacy Thesaurus, Application Domain, Technology Topic, Popular Technical Reports.
© 2024 PatSnap. All rights reserved.Legal|Privacy policy|Modern Slavery Act Transparency Statement|Sitemap|About US| Contact US: help@patsnap.com