Polishing device for precision casting and positioning and clamping mechanism of polishing device
A technology of precision casting and clamping mechanism, which is applied to grinding drive device, grinding/polishing safety device, grinding frame, etc. Good grinding effect, high precision, avoid random scattering effect
- Summary
- Abstract
- Description
- Claims
- Application Information
AI Technical Summary
Problems solved by technology
Method used
Image
Examples
Embodiment 1
[0047] see Figure 1-4 , the present invention provides a technical solution: a positioning and clamping mechanism, which is applied to a precision casting grinding device, comprising:
[0048] The workbench 200, the upper end of the workbench 200 is provided with two sets of first slide rails 210 at intervals, each set of the first slide rails 210 is slidably connected with two sets of moving blocks 211, and the upper end of the moving blocks 211 is provided with a telescopic column 220, and the telescopic column 220 is A spring 221 is wound around, a carrier plate 230 is connected to the upper end of the telescopic column 220, and a frame plate 231 is arranged on the upper end of the carrier plate 230. There are rubber sheets;
[0049] The fixing frame 250, the fixing frame 250 is arranged on the upper end of the workbench 200, and is located on the rear side of the two sets of bearing plates 230, a movable plate 251 is movably arranged in the middle of the fixing frame 250...
Embodiment 2
[0055] see Figure 1-4 , the present invention provides a technical solution: a positioning and clamping mechanism, which is applied to a precision casting grinding device, comprising:
[0056] The workbench 200, the upper end of the workbench 200 is provided with two sets of first slide rails 210 at intervals, each set of the first slide rails 210 is slidably connected with two sets of moving blocks 211, and the upper end of the moving blocks 211 is provided with a telescopic column 220, and the telescopic column 220 is A spring 221 is wound around, a carrier plate 230 is connected to the upper end of the telescopic column 220, and a frame plate 231 is arranged on the upper end of the carrier plate 230. There are rubber sheets;
[0057] The fixing frame 250, the fixing frame 250 is arranged on the upper end of the workbench 200, and is located on the rear side of the two sets of bearing plates 230, a movable plate 251 is movably arranged in the middle of the fixing frame 250...
Embodiment 3
[0064] see Figure 1-10 , the present invention also provides the following technical solutions: a grinding device for precision castings, comprising:
[0065] The base 100, the front side of the base 100 is provided with a back plate 120, the two ends of the back plate 120 are connected with side plates 110, the side walls of the base 100 of the side plate 110 extend backward, and the base 100 is connected with the back plate 120 and the side plate 110. The material chute 130; the collection chute 130 is provided with a collection box 131, the collection box 131 is inclined with a material guide plate on the side close to the scraper mechanism 400, and the back plate 120 and the side plate 110 are respectively provided with through holes for Pick and place the collection box 131 in the collection tank 130;
[0066] A positioning and clamping mechanism in Embodiment 1 or Embodiment 2, which is arranged in the middle of the upper end of the base 100;
[0067] The grinding mec...
PUM
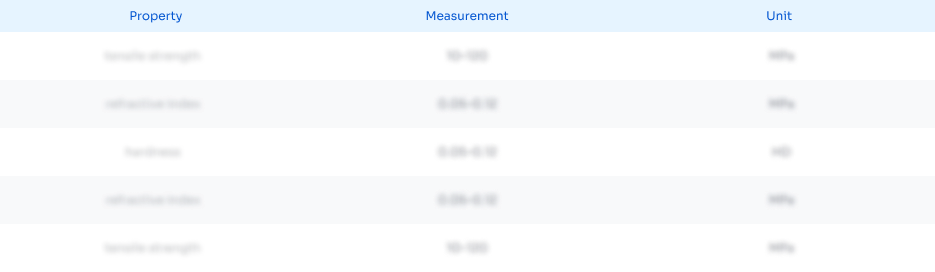
Abstract
Description
Claims
Application Information

- R&D
- Intellectual Property
- Life Sciences
- Materials
- Tech Scout
- Unparalleled Data Quality
- Higher Quality Content
- 60% Fewer Hallucinations
Browse by: Latest US Patents, China's latest patents, Technical Efficacy Thesaurus, Application Domain, Technology Topic, Popular Technical Reports.
© 2025 PatSnap. All rights reserved.Legal|Privacy policy|Modern Slavery Act Transparency Statement|Sitemap|About US| Contact US: help@patsnap.com