Production method of high-performance cladding coating on surface of aluminum alloy
An aluminum alloy surface, high-performance technology, applied in the direction of metal material coating process, coating, etc., to achieve the effect of low cost, enhanced comprehensive performance, and improved lifespan
- Summary
- Abstract
- Description
- Claims
- Application Information
AI Technical Summary
Problems solved by technology
Method used
Examples
Embodiment 1
[0034] 1. Working with 300 golden phase sandpaper using 300, then performing surface sandblasting treatment.
[0035] 2. Clean the aluminum alloy surface with acetone and then washed 1 h in an ultrasonic cleaning machine.
[0036] 3. Preparation of mucous powder: 92% Ni60, 1% SiC and 7% LA with mass fraction 2 O 3 The ball mill is placed in the planetary ball mill, wherein the ball mill is: the rotational speed is 300r / min, the ball ratio is 5: 1, the time is 2 h, the diameter is 3mm, 5 mm, and the ratio of stainless steel ball ratio of 8 mm is 3: 5: 2 The ball milling process is carried out under argon atmosphere protection.
[0037] 4, the mixed powder after the ball is prepared into a paste and is uniformly applied to the surface-treated aluminum alloy surface with a thickness of about 1 mm. Then dry 1 h at 120 ° C.
[0038] 5. The coating layer is coldly pressed into a prefabricated block using a hydraulic device, wherein the cold pressure pressure is 30 MPa, and the holding...
Embodiment 2
[0042] 1. Working with 300 golden phase sandpaper using 300, then performing surface sandblasting treatment.
[0043] 2. Clean the aluminum alloy surface with acetone and washed 1.5 h in an ultrasonic cleaning machine.
[0044] 3. Preparation of mucous powder: 94% Ni60, 1% SiC and 5% LA with mass fraction 2 O 3 The ball mill is placed in the planetary ball mill, wherein the ball mill is: the rotational speed is 400r / min, the ball ratio is 5: 1, the time is 2 h, the diameter is 3mm, 5 mm, 8 mm stainless steel ball ratio is 3: 5: 2 The ball milling process is carried out under argon atmosphere protection.
[0045] 4, the mixed powder after ball mill is prepared into a paste, and is uniformly coated with a surface-treated aluminum alloy surface with a thickness of about 1.5 mm. Then dry at 140 ° C for 1 h.
[0046] 5. The coating layer is coldly pressed into a prefabricated block using a hydraulic device, wherein the cold pressure pressure is 40 MPa, and the holding time is 40 min....
Embodiment 3
[0050] 1. Working with 200 of the aluminum alloy surface to be credited using 200, then perform surface sandblasting treatment.
[0051] 2. Clean the aluminum alloy surface with acetone and washed 1.5 h in an ultrasonic cleaning machine.
[0052] 3. Preparation of mucous powder: 92% Ni60, 2% SiC and 6% LA with mass fraction 2 O 3 The ball mill is placed in the planetary ball mill, wherein the ball milling parameters are: the rotational speed is 400r / min, the ball ratio is 5: 1, the time is 3 h, 3mm, 5 mm, 8 mm, respectively, 3: 5: 2 The ball milling process is carried out under argon atmosphere protection.
[0053] 4, the mixed powder after ball mill is prepared into a paste, and is uniformly coated with a surface-treated aluminum alloy surface with a thickness of about 1.5 mm. Then dry at 140 ° C for 1 h.
[0054] 5. The coating layer is coldly pressed into a prefabricated block using a hydraulic device, wherein the cold pressure pressure is 50 MPa, and the holding time is 25 m...
PUM
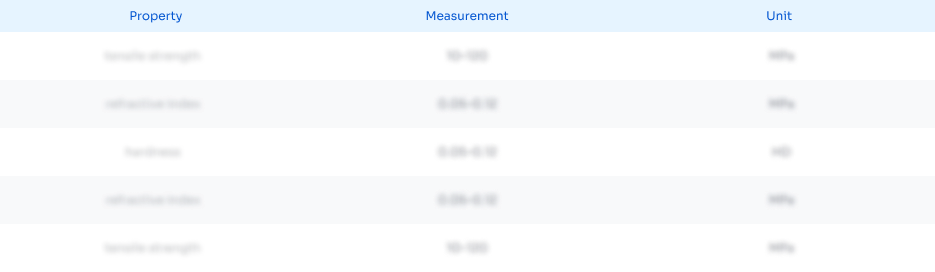
Abstract
Description
Claims
Application Information

- Generate Ideas
- Intellectual Property
- Life Sciences
- Materials
- Tech Scout
- Unparalleled Data Quality
- Higher Quality Content
- 60% Fewer Hallucinations
Browse by: Latest US Patents, China's latest patents, Technical Efficacy Thesaurus, Application Domain, Technology Topic, Popular Technical Reports.
© 2025 PatSnap. All rights reserved.Legal|Privacy policy|Modern Slavery Act Transparency Statement|Sitemap|About US| Contact US: help@patsnap.com