Grinding mechanism for pulverized coal production
A technology of grinding mechanism and pulverized coal, which is used in dryers, drying solid materials, heating devices, etc., can solve the problems of poor grinding effect of the grinding machine, inability to grind pulverized coal uniformly, and sparks generated when grinding pulverized coal, and avoid the Dry dead corners exist, avoid bunching, and improve the grinding effect
- Summary
- Abstract
- Description
- Claims
- Application Information
AI Technical Summary
Problems solved by technology
Method used
Image
Examples
Embodiment Construction
[0028] The present invention will be further described below in conjunction with the accompanying drawings and specific embodiments.
[0029] A grinding mechanism for pulverized coal production, comprising a crushing device 1, a fine grinding device 2 communicated with the crushing device 1 through a first pipeline, and a drying device 3 communicated with the fine grinder 2 through a second pipeline;
[0030] The crushing device 1 includes a cylinder 4, a crushing shaft 5 installed on the cylinder 4 through a rolling bearing, a crushing motor 6 installed on the cylinder 4 and the output shaft connected to the crushing shaft 5, and a plurality of motors installed on the crushing shaft 5. smashing knife 7;
[0031] The cylinder body 4 is provided with a material inlet and a material outlet, and the material outlet is connected with the first pipeline.
[0032] The coal is crushed by the crushing device 1 to prepare for the work of the fine grinding device 2 .
[0033] The fine...
PUM
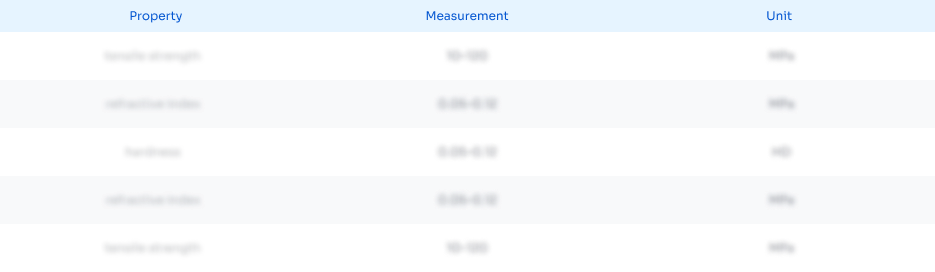
Abstract
Description
Claims
Application Information

- R&D
- Intellectual Property
- Life Sciences
- Materials
- Tech Scout
- Unparalleled Data Quality
- Higher Quality Content
- 60% Fewer Hallucinations
Browse by: Latest US Patents, China's latest patents, Technical Efficacy Thesaurus, Application Domain, Technology Topic, Popular Technical Reports.
© 2025 PatSnap. All rights reserved.Legal|Privacy policy|Modern Slavery Act Transparency Statement|Sitemap|About US| Contact US: help@patsnap.com