Production process of aluminum alloy gutter profile
A production process, aluminum alloy technology, applied in the production process field of aluminum alloy gutter profiles, can solve problems such as lack of strength
- Summary
- Abstract
- Description
- Claims
- Application Information
AI Technical Summary
Problems solved by technology
Method used
Image
Examples
Embodiment 1
[0015] S1, the ingot casting process, the aluminum ingot is melted and poured into the mold to form a bar
[0016] S2. Preliminary heat treatment process, heating the bar to 580°C, then keeping it warm for 3 hours, and cooling it quickly to 25°C by spraying water mist after it is released from the furnace;
[0017] S3. Extrusion molding process, the bar is extruded through the extruder equipment, the bar is heated to 475°C, the temperature of the extrusion barrel of the extruder is 400°C, the temperature of the forming die is 465°C, and the extrusion speed is controlled at 7m / min;
[0018] S4, stretching and straightening process, the stretching deformation rate is controlled to 1%;
[0019] S5, the quenching process, adopts the online quenching method;
[0020] S6, aging treatment process, heating to 190° C. and holding for 2 hours to obtain the final product.
Embodiment 2
[0022] S1, the ingot casting process, the aluminum ingot is melted and poured into a mold to form a bar;
[0023] S2. Preliminary heat treatment process, heating the bar to 595°C, then keeping it warm for 6 hours, and cooling it quickly to 30°C by spraying water mist after it is released from the furnace;
[0024] S3. Extrusion molding process, the bar is extruded through the extruder equipment, the bar is heated to 495°C, the temperature of the extrusion barrel of the extruder is 420°C, the temperature of the forming die is 485°C, and the extrusion speed is controlled at 8m / min;
[0025] S4, stretching and straightening process, the stretching deformation rate is controlled at 2%;
[0026] S5, the quenching process, adopts the online quenching method;
[0027] S6, the aging treatment process, heating to 200° C. and keeping it warm for 3 hours to obtain the final product.
Embodiment 3
[0029] S1, the ingot casting process, the aluminum ingot is melted and poured into a mold to form a bar;
[0030] S2. Preliminary heat treatment process, heating the bar to 585°C, then keeping it warm for 4 hours, and cooling it quickly to 27°C by spraying water mist after it is released from the furnace;
[0031] S3. Extrusion molding process, the bar is extruded through the extruder equipment, the bar is heated to 485°C, the temperature of the extrusion barrel of the extruder is 410°C, the temperature of the forming die is 475°C, and the extrusion speed is controlled at 8m / min;
[0032] S4, stretching and straightening process, the stretching deformation rate is controlled at 1.5%;
[0033] S5, the quenching process, adopts the online quenching method;
[0034] S6, the aging treatment process, heating to 195° C. and keeping the temperature for 2.5 hours to obtain the final product.
PUM
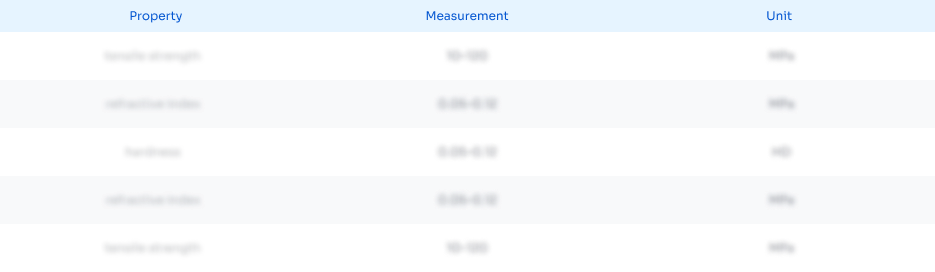
Abstract
Description
Claims
Application Information

- R&D
- Intellectual Property
- Life Sciences
- Materials
- Tech Scout
- Unparalleled Data Quality
- Higher Quality Content
- 60% Fewer Hallucinations
Browse by: Latest US Patents, China's latest patents, Technical Efficacy Thesaurus, Application Domain, Technology Topic, Popular Technical Reports.
© 2025 PatSnap. All rights reserved.Legal|Privacy policy|Modern Slavery Act Transparency Statement|Sitemap|About US| Contact US: help@patsnap.com