Functional modified silicon dioxide flame-retardant modified polylactic acid composite fiber and preparation method thereof
A technology of silica and composite fibers, which is applied in the manufacture of fire-retardant and flame-retardant filaments, chemical characteristics of fibers, and rayon manufacturing. shedding effect
- Summary
- Abstract
- Description
- Claims
- Application Information
AI Technical Summary
Problems solved by technology
Method used
Image
Examples
preparation example Construction
[0028] In order to achieve the above object, the present invention provides the following specific embodiments and examples: a functionalized modified silica flame retardant modified polylactic acid composite fiber, the preparation method comprising the following steps:
[0029] (1) Add acetonitrile solvent and nano silicon dioxide to the reactor, ultrasonically disperse evenly, continue to add adipic acid, wherein the mass ratio of acetonitrile solvent, nano silicon dioxide and adipic acid is 450-1200:10:15-40 , mix evenly, transfer to an oil bath, raise the temperature to 70-90°C, stir and react at a constant temperature for 12-36h, centrifuge, wash and dry after the reaction to obtain carboxylated silica;
[0030] (2) Add tetrahydrofuran solvent and carboxylated silica into the reactor, ultrasonically disperse for 10-30min, continue to add hydroxyl-terminated nitrile rubber and dicyclohexyl carbodiimide, wherein tetrahydrofuran solvent, carboxylated silica, terminal The mas...
Embodiment 1
[0035] (1) Add 290mL of acetonitrile solvent and 5g of nano-silica to the reactor, ultrasonically disperse evenly, continue to add 7.5g of adipic acid, mix evenly, transfer to an oil bath, raise the temperature to 70°C, and stir at a constant temperature for reaction 12h, centrifuged after the reaction, washed and dried to obtain carboxylated silicon dioxide;
[0036] (2) Add 340mL tetrahydrofuran solvent and 5g carboxylated silica into the reactor, ultrasonically disperse for 10min, continue to add 6g hydroxy-terminated nitrile rubber and 15g dicyclohexylcarbodiimide, stir mechanically and transfer to the oil bath , stirred and reacted at 20°C for 12 hours, precipitated after the reaction, filtered with suction, washed and dried to obtain hydroxy-terminated nitrile rubber-modified silica;
[0037] (3) Add 270mL of n-hexane solvent and 5g of hydroxy-terminated nitrile rubber modified silica into the reactor, ultrasonically disperse until completely dissolved, continue to add 0...
Embodiment 2
[0041] (1) Add 360mL of acetonitrile solvent and 5g of nano-silica into the reactor, ultrasonically disperse evenly, continue to add 11g of adipic acid, mix evenly, transfer to an oil bath, raise the temperature to 75°C, and stir at a constant temperature for 16h , centrifuging, washing and drying after the reaction to obtain carboxylated silicon dioxide;
[0042] (2) Add 500mL tetrahydrofuran solvent and 5g carboxylated silica into the reactor, ultrasonically disperse for 15min, continue to add 7.5g hydroxyl-terminated nitrile rubber and 20g dicyclohexyl carbodiimide, mechanically stir evenly and transfer to an oil bath In a pot, stir and react at 25°C for 15 hours, precipitate after the reaction, filter with suction, wash and dry to obtain hydroxy-terminated nitrile rubber-modified silica;
[0043] (3) Add 400mL of n-hexane solvent and 5g of hydroxy-terminated nitrile rubber modified silica into the reactor, ultrasonically disperse until completely dissolved, continue to add...
PUM
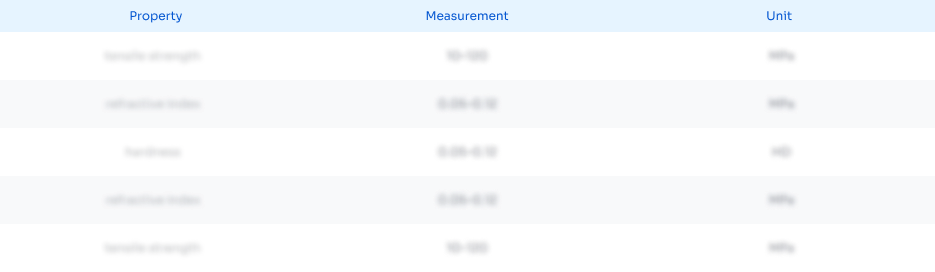
Abstract
Description
Claims
Application Information

- R&D Engineer
- R&D Manager
- IP Professional
- Industry Leading Data Capabilities
- Powerful AI technology
- Patent DNA Extraction
Browse by: Latest US Patents, China's latest patents, Technical Efficacy Thesaurus, Application Domain, Technology Topic, Popular Technical Reports.
© 2024 PatSnap. All rights reserved.Legal|Privacy policy|Modern Slavery Act Transparency Statement|Sitemap|About US| Contact US: help@patsnap.com