Microassembling robot system based on microvision
A robotic system and microscopic vision technology, applied in the field of robotics, can solve problems such as limited movement space, low reliability and efficiency, and inability to meet the three-dimensional space movement range, and achieve reliable absorption and release, convenient operation, application prospects and society. considerable economic benefits
- Summary
- Abstract
- Description
- Claims
- Application Information
AI Technical Summary
Problems solved by technology
Method used
Image
Examples
Embodiment Construction
[0015] Such as figure 1 As shown, the present invention is composed of a system control host 1, a manipulator controller 2, a micromanipulator 3, a vacuum microclamp controller 4, a vacuum microclamp 5, an image acquisition card 7 and a microscope 8 with a camera, and the micromanipulator 3 , vacuum micro-clip 5 and microscope 8 are connected to the system control host 1 through the manipulator controller 2, the vacuum micro-clip controller 4 and the image acquisition card 7 respectively. The vacuum micro-clamp can operate on particulate objects placed on the operating platform 6 . Wherein, the system control host 1, the manipulator controller 2, and the vacuum micro-clip controller 4 constitute the controller part of the present invention, and the image acquisition card 7 and the microscope 8 with a camera constitute the microscopic vision part of the present invention.
[0016] In this embodiment, the operating manipulator 3 is composed of multiple micro-motion platforms, a...
PUM
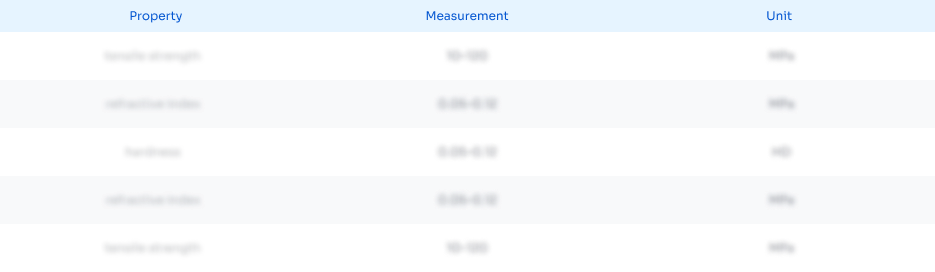
Abstract
Description
Claims
Application Information

- R&D
- Intellectual Property
- Life Sciences
- Materials
- Tech Scout
- Unparalleled Data Quality
- Higher Quality Content
- 60% Fewer Hallucinations
Browse by: Latest US Patents, China's latest patents, Technical Efficacy Thesaurus, Application Domain, Technology Topic, Popular Technical Reports.
© 2025 PatSnap. All rights reserved.Legal|Privacy policy|Modern Slavery Act Transparency Statement|Sitemap|About US| Contact US: help@patsnap.com