Workpiece alignment method and device for secondary clamping of machine tool and computer storage medium
A secondary clamping and workpiece technology, applied in the field of CNC machine tools, can solve the problems of low manual measurement accuracy, insufficient stability, lack of versatility, etc., to solve the problem of correcting the position and posture of the workpiece, reduce labor intensity, and reduce measurement time Effect
- Summary
- Abstract
- Description
- Claims
- Application Information
AI Technical Summary
Problems solved by technology
Method used
Image
Examples
Embodiment Construction
[0054] The following will clearly and completely describe the technical solutions in the embodiments of the present application with reference to the accompanying drawings in the embodiments of the present application. Obviously, the described embodiments are only part of the embodiments of the present application, not all of them. Based on the embodiments in this application, all other embodiments obtained by persons of ordinary skill in the art without making creative efforts belong to the scope of protection of this application.
[0055]The workpiece alignment method of the secondary clamping of the machine tool in the embodiment of the present application can be applied to a five-axis linkage machine tool. The five-axis linkage machine tool is based on the traditional three-axis machine tool (three linear axes) with two rotation axes. In this way, the ability to process complex curved surfaces is obtained, and it is widely used in the processing of high-precision workpieces...
PUM
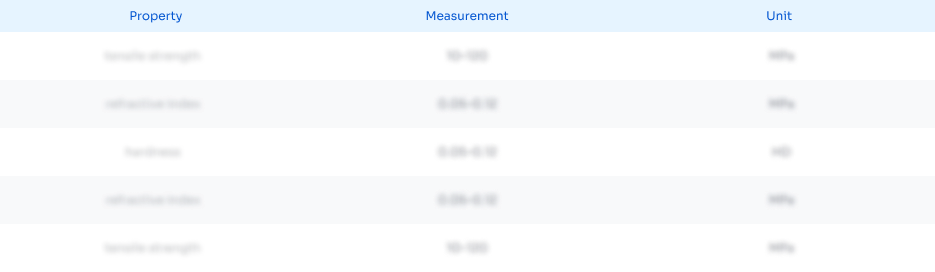
Abstract
Description
Claims
Application Information

- Generate Ideas
- Intellectual Property
- Life Sciences
- Materials
- Tech Scout
- Unparalleled Data Quality
- Higher Quality Content
- 60% Fewer Hallucinations
Browse by: Latest US Patents, China's latest patents, Technical Efficacy Thesaurus, Application Domain, Technology Topic, Popular Technical Reports.
© 2025 PatSnap. All rights reserved.Legal|Privacy policy|Modern Slavery Act Transparency Statement|Sitemap|About US| Contact US: help@patsnap.com