Production process of double-sided antistatic ultralight release film and release film
A production process and anti-static technology, which is applied to devices for coating liquid on surfaces, special surfaces, conductive coatings, etc. The problem of poor antistatic effect of the film can improve the antistatic function, increase the thickness and improve the adhesion.
- Summary
- Abstract
- Description
- Claims
- Application Information
AI Technical Summary
Problems solved by technology
Method used
Image
Examples
Embodiment 1
[0024] Antistatic lightweight sided release film comprising a base film layer, the base film layer is provided on both sides, and an antistatic layer disposed on at least a release layer, an antistatic layer is coated with an antistatic layer on the surface of an antistatic coating solution cured layer obtained, the release layer is made of a release agent coating solution prepared coating is cured;
[0025] Parts by mass of the constituent releasing agent coating solution comprising 100 parts of a main agent from Dow Corning silicone oil SL9106-, hydrogen-containing cyclic polydimethylsiloxanes V60 Wacker 4 parts of polydimethylsiloxane 6 parts of Dow Corning 7200, Dow Corning 4000 platinum catalyst, 5 parts by Shin-Etsu KMP590 3.5 parts of silica, 4 parts of ethynyl cyclohexanol PLR2 Topco Technology, 3 parts of a silane coupling agent SE9176 of Dow Corning, Dow Corning 100 silicone oil, 9106 parts of toluene, SK / petrochemical 60 parts, 40 parts of methyl ethyl ketone SK Korea...
Embodiment 2
[0038]Example 2 Based on Example 1, the difference is that the main agent released silicone oil is a WACK SF500.
Embodiment 3
[0040] Example 3 According to Example 1, the difference is that the coating amount of the released agent coating liquid is 5.6 g / m. 2 The layer thickness of the lactation layer is 2.5 μm after curing.
PUM
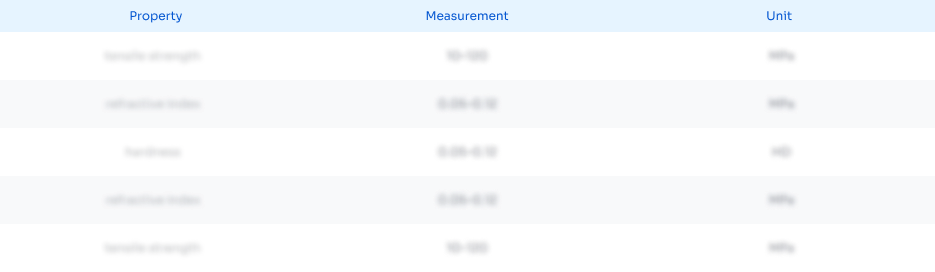
Abstract
Description
Claims
Application Information

- R&D Engineer
- R&D Manager
- IP Professional
- Industry Leading Data Capabilities
- Powerful AI technology
- Patent DNA Extraction
Browse by: Latest US Patents, China's latest patents, Technical Efficacy Thesaurus, Application Domain, Technology Topic, Popular Technical Reports.
© 2024 PatSnap. All rights reserved.Legal|Privacy policy|Modern Slavery Act Transparency Statement|Sitemap|About US| Contact US: help@patsnap.com