A kind of preparation method of high-performance composite membrane material special for alkaline battery
A composite diaphragm and alkaline battery technology, which is applied to battery pack parts, circuits, electrical components, etc., can solve the problems of small diameter of diaphragm paper fibers, poor quality of diaphragm paper, and high production cost, and achieve good alkali retention rate and thickness The effect of poor uniformity and high processing current
- Summary
- Abstract
- Description
- Claims
- Application Information
AI Technical Summary
Problems solved by technology
Method used
Examples
Embodiment 1
[0034] Preparation of modified silicone composite antifoam agent emulsion:
[0035] Step S21. Mix allyl polyoxyethylene polyoxypropylene ether, butyl acrylate and low-hydrogen silicone oil, and add the isopropanol solution of chloroplatinic acid dropwise at a temperature of 85°C. After the dropwise addition, React for 8 hours to obtain the organosilicon mother liquor;
[0036] Step S22, mix the silicone mother liquor and white carbon black, and heat under reflux at 150°C for 5 hours to obtain a paste; mix graphene oxide, dimethyl silicone oil and hydroxyl silicone oil at a speed of 8000r / min Under the condition of shear homogeneity for 40min, graphene oxide modified silicone oil was obtained;
[0037] Step S23, mix the paste and graphene oxide modified silicone oil, cut for 40 minutes at a rotation speed of 8000r / min, add sorbitan fatty acid ester, cut for 15 minutes at a temperature of 40°C, and then add Deionized water was sheared for 60 minutes, and finally γ-aminopropylt...
Embodiment 2
[0042] To prepare the surface size:
[0043] Step S11, mixing sodium carboxymethyl cellulose and deionized water according to the mass ratio of 0.5:100 to obtain a mixed solution A; adding water to polyvinyl alcohol and steaming for aging, controlling the mass concentration at 8% to obtain a mixed solution B ;Mix the non-ionic surfactant and deionized water according to the mass ratio of 7:100 to obtain the mixed liquid C;
[0044] Step S12, mixing the mixed solution A, the mixed solution B and the mixed solution C according to a volume ratio of 1:1:1 to obtain a surface sizing agent.
[0045] Wherein, the nonionic surfactant is fatty alcohol polyoxyethylene ether.
Embodiment 3
[0047] To prepare the surface size:
[0048] Step S11, mixing sodium carboxymethyl cellulose and deionized water according to the mass ratio of 0.8:100 to obtain a mixed solution A; adding water to polyvinyl alcohol and steaming for aging, controlling the mass concentration at 9% to obtain a mixed solution B ;Mix the non-ionic surfactant and deionized water according to the mass ratio of 7:100 to obtain the mixed liquid C;
[0049] Step S12, mixing the mixed solution A, the mixed solution B and the mixed solution C according to the volume ratio of 1:1:2 to obtain a surface sizing agent.
[0050] Wherein, the nonionic surfactant is alkylphenol polyoxyethylene ether.
PUM
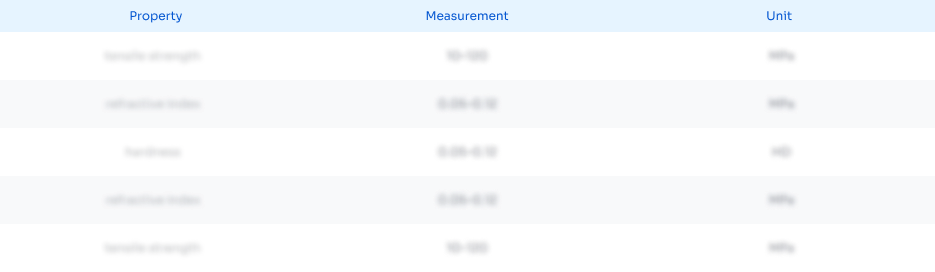
Abstract
Description
Claims
Application Information

- R&D
- Intellectual Property
- Life Sciences
- Materials
- Tech Scout
- Unparalleled Data Quality
- Higher Quality Content
- 60% Fewer Hallucinations
Browse by: Latest US Patents, China's latest patents, Technical Efficacy Thesaurus, Application Domain, Technology Topic, Popular Technical Reports.
© 2025 PatSnap. All rights reserved.Legal|Privacy policy|Modern Slavery Act Transparency Statement|Sitemap|About US| Contact US: help@patsnap.com