Multi-element recycling of residual oil hydrogenation waste catalyst
A technology for hydrogenation of spent catalysts and residual oil, applied in chemical recovery, nickel oxide/nickel hydroxide, aluminum oxide/aluminum hydroxide, etc., can solve problems such as poor working conditions, high energy consumption, and heavy pollution, and achieve The effects of avoiding operations, low energy consumption, and less secondary hazardous waste
- Summary
- Abstract
- Description
- Claims
- Application Information
AI Technical Summary
Problems solved by technology
Method used
Image
Examples
Embodiment Construction
[0055] The following will clearly and completely describe the technical solutions in the embodiments of the present invention with reference to the accompanying drawings in the embodiments of the present invention. Obviously, the described embodiments are only some, not all, embodiments of the present invention. Based on the embodiments of the present invention, all other embodiments obtained by persons of ordinary skill in the art without making creative efforts belong to the protection scope of the present invention.
[0056] see figure 1 , in the embodiment of the present invention, the multi-element recovery and utilization of residual oil hydrogenation waste catalyst, its multi-element recovery and utilization method is the following steps:
[0057] S1. Add a certain proportion of sodium carbonate and water to the waste catalyst, stir it evenly, and send it into the rotary kiln, and use natural gas as a combustion aid, and roast it at high temperature in the rotary kiln. ...
PUM
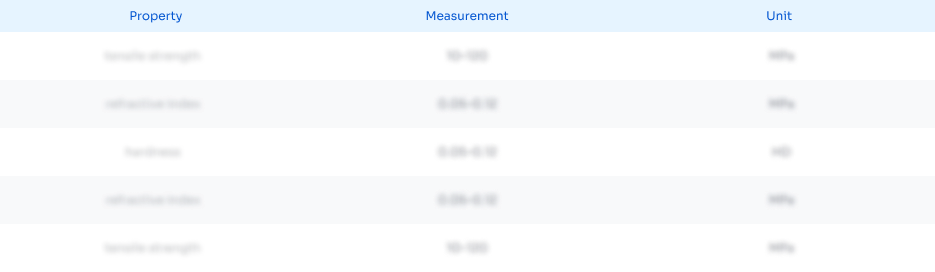
Abstract
Description
Claims
Application Information

- R&D
- Intellectual Property
- Life Sciences
- Materials
- Tech Scout
- Unparalleled Data Quality
- Higher Quality Content
- 60% Fewer Hallucinations
Browse by: Latest US Patents, China's latest patents, Technical Efficacy Thesaurus, Application Domain, Technology Topic, Popular Technical Reports.
© 2025 PatSnap. All rights reserved.Legal|Privacy policy|Modern Slavery Act Transparency Statement|Sitemap|About US| Contact US: help@patsnap.com