Rolling method for wide metal strap foil
A metal strip and wide-width technology, applied in the directions of metal rolling, metal rolling, metal rolling stands, etc., can solve the problems of low rigidity, unsuitable for thinning, restricting high-precision wide-width strip and foil rolling, etc. Curl deformation problem, effect in favor of thinning, significant application value and economic value
- Summary
- Abstract
- Description
- Claims
- Application Information
AI Technical Summary
Problems solved by technology
Method used
Image
Examples
Embodiment 1
[0053] The invention discloses a rolling method of wide-width metal strip and foil, which is used for rolling copper alloy strip and foil. The final rolling thickness of the copper alloy strip and foil is 0.01mm, and the width is 800mm. The boundary thickness of the strip and the foil is 0.15mm, and the thickness of the copper alloy strip and foil (hereinafter referred to as the strip foil) already belongs to the foil. Due to the high deformation resistance of copper alloy, it is difficult to ensure the flatness of its plate shape.
[0054] Such as Figure 5 As shown, a flattening roller 3 is arranged on the entrance side of the roll gap, and the roll surface of the flattening roller 3 is lower than the rolling centerline 6. After the strip foil 5 passes through the front stretching of the flattening roller 3, it enters obliquely upwards and is formed by a pair of working rollers. In the roll gap formed by the rolls, the roll diameter of the upper work roll 1 is 30 mm, the ro...
Embodiment 2
[0069] Such as Figure 12 As shown, the difference between this embodiment and Embodiment 1 is that the strip foil 5 enters the roll gap horizontally along the rolling centerline 6, and a flattening roll 3 is arranged on the exit side of the roll gap, and the roll surface of the flattening roll 3 is as high as On the rolling centerline 6. The flattening roller 3 post-stretches the strip foil 5 so that the strip foil 5 forms an exit-side cladding arc on the roll surface of the upper working roll 1, and the cladding angle of the exit-side cladding arc is β, and β is also 30°. Due to the existence of the wrapping arc on the exit side, the upper work roll 1 backs up the strip foil 5, and the tension is evenly distributed on the cross section of the wrapping arc on the exit side. The principle is as follows:
[0070] Such as Figure 13 As shown, the strip foil 5 flowing out from the roll gap is wrapped on the upper work roll 1 to form an outlet-side wrapping arc. Since the linea...
Embodiment 3
[0075] This embodiment can be regarded as a combination of Embodiment 1 and Embodiment 2, such as Figure 14 As shown, the strip foil 5 forms an entry-side cladding arc with the lower work roll 2 on the entrance side of the roll gap, and the cladding angle α of the entrance-side cladding arc is 30°; the strip foil 5 works on the exit side and the upper work roll of the roll gap The roll 1 forms an exit-side cladding arc, and the cladding angle β of the exit-side cladding arc is also 30°. Due to the existence of the entrance-side cladding arc and the exit-side cladding arc, the lower work roll 2 and the upper work roll 1 respectively produce back support for the strip foil 5 .
[0076] The function and influence of the cladding arc on the entrance side in rolling has been explained in Example 1, and the function and influence of the cladding arc on the exit side in rolling has been explained in Example 2, so it will not be repeated here. It is worth noting that if Figure 13 ...
PUM
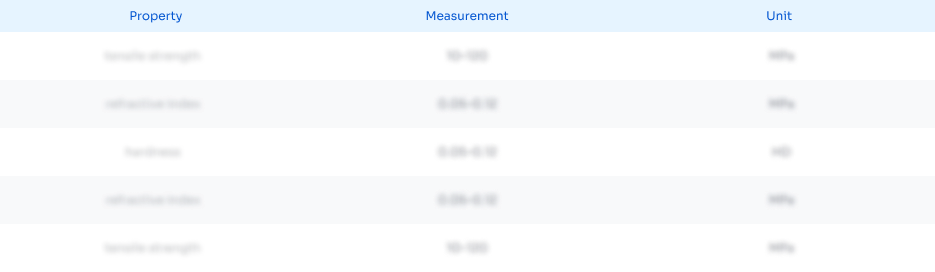
Abstract
Description
Claims
Application Information

- Generate Ideas
- Intellectual Property
- Life Sciences
- Materials
- Tech Scout
- Unparalleled Data Quality
- Higher Quality Content
- 60% Fewer Hallucinations
Browse by: Latest US Patents, China's latest patents, Technical Efficacy Thesaurus, Application Domain, Technology Topic, Popular Technical Reports.
© 2025 PatSnap. All rights reserved.Legal|Privacy policy|Modern Slavery Act Transparency Statement|Sitemap|About US| Contact US: help@patsnap.com