Method for preparing laser cladding layer of cutting edge of cutter based on powder-cored wire deep penetration mode
A laser cladding, powder core wire technology, applied in coating, metal material coating process and other directions, can solve the problem of low deposition efficiency, achieve the effect of excellent performance, increase melting efficiency, and reduce melting amount
- Summary
- Abstract
- Description
- Claims
- Application Information
AI Technical Summary
Problems solved by technology
Method used
Image
Examples
Embodiment 1
[0037] This embodiment provides a method for preparing a laser cladding layer on a cutting edge based on a powder core wire material deep fusion mode, including:
[0038] The powder-cored welding wire and the laser beam are arranged on both sides of the normal line of the cutting edge plane at a certain angle.
[0039] The shielding gas is loaded coaxially with the powder cored wire, and the flow direction of the shielding gas is consistent with the feeding direction of the powder cored wire.
[0040] The laser beam is directly applied to the surface of the powder-cored welding wire in a certain defocused state, and the position of the spot is separated from the cutting edge substrate by a certain distance, so that the powder-cored welding wire melts in a deep melting mode and transitions to the cutting edge substrate below surface, forming a cladding layer.
[0041] In a preferred embodiment, the laser spot diameter of the laser beam acting on the surface of the powder cored...
Embodiment 2
[0054] This embodiment provides a tool edge laser cladding system, including:
[0055] A wire feeding device capable of feeding powder-cored welding wire to the cutting edge of the tool;
[0056] A laser output device, which is set so that the powder cored wire and the laser beam are arranged at a certain angle on both sides of the normal line of the cutting edge plane;
[0057] The wire feeding device is a coaxial shielded wire feeding device, which is set so that the shielding gas is loaded coaxially with the powder cored wire, and the flow direction of the shielding gas is consistent with the feeding direction of the powder cored wire;
[0058] The laser beam of the laser output device directly acts on the surface of the powder-cored welding wire in a certain defocused state, and the position of the light spot is separated from the base material of the cutting edge by a certain distance, so that the powder-cored welding wire melts in a deep melting mode and transitions to t...
PUM
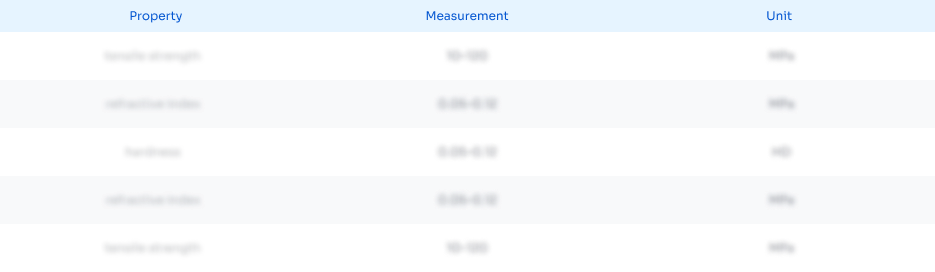
Abstract
Description
Claims
Application Information

- Generate Ideas
- Intellectual Property
- Life Sciences
- Materials
- Tech Scout
- Unparalleled Data Quality
- Higher Quality Content
- 60% Fewer Hallucinations
Browse by: Latest US Patents, China's latest patents, Technical Efficacy Thesaurus, Application Domain, Technology Topic, Popular Technical Reports.
© 2025 PatSnap. All rights reserved.Legal|Privacy policy|Modern Slavery Act Transparency Statement|Sitemap|About US| Contact US: help@patsnap.com