Modification and optimization method of iridium dioxide catalyst
A technology of iridium dioxide and optimization method, which is applied in the direction of electrodes, electrolysis process, electrolysis components, etc., to achieve the effect of improving catalytic oxygen evolution performance, improving oxygen evolution catalytic performance, and reducing the content of elemental iridium
- Summary
- Abstract
- Description
- Claims
- Application Information
AI Technical Summary
Problems solved by technology
Method used
Examples
Embodiment 1
[0025] First, the 8 cm × 6 cm boat was sonicated for 30 min with ethanol and deionized water, respectively, and dried in an oven for use.
[0026] Weigh 3 g of commercial iridium dioxide catalyst, place it in a clean burning boat, and spread the catalyst evenly on the bottom surface of the burning boat. Place the burning boat containing the catalyst in the middle of the tube furnace, in an air atmosphere, at a heating rate of 5 °C / min, heat up to 700 °C for 3 hours, after the heat treatment, cool down to room temperature with the furnace, take out The catalyst sample was tested by X-ray diffractometer, and the results showed that the characteristic peak position of the sample was similar to that of standard IrO 2 The peaks are consistent, so it is known that the iridium dioxide catalyst is prepared in this example.
Embodiment 2
[0028] First, the 8 cm × 6 cm boat was sonicated for 30 min with ethanol and deionized water, respectively, and dried in an oven for use.
[0029] Weigh 3 g of commercial iridium dioxide catalyst, place it in a clean burning boat, and spread the catalyst evenly on the bottom surface of the burning boat. Place the burning boat containing the catalyst in the middle of the tube furnace, in an air atmosphere, at a heating rate of 2 °C / min, heat up to 900 °C for 2 hours, after the heat treatment, cool down to room temperature with the furnace, take out The catalyst sample was tested by X-ray diffractometer, and the results showed that the characteristic peak position of the sample was similar to that of standard IrO 2 The peaks are consistent, so it is known that the iridium dioxide catalyst is prepared in this example.
Embodiment 3
[0031] First, the 8 cm × 6 cm boat was sonicated for 30 min with ethanol and deionized water, respectively, and dried in an oven for use.
[0032] Weigh 5g of commercial iridium dioxide catalyst, place it in a clean burning boat, and spread the catalyst evenly on the bottom surface of the burning boat. Place the burning boat containing the catalyst in the middle of the tube furnace, in an air atmosphere, at a heating rate of 2 °C / min, heat up to 700 °C for 5 hours, and after the heat treatment, cool down to room temperature with the furnace, take out The catalyst sample was tested by X-ray diffractometer, and the results showed that the characteristic peak position of the sample was similar to that of standard IrO 2 The peaks are consistent, so it is known that the iridium dioxide catalyst is prepared in this example.
PUM
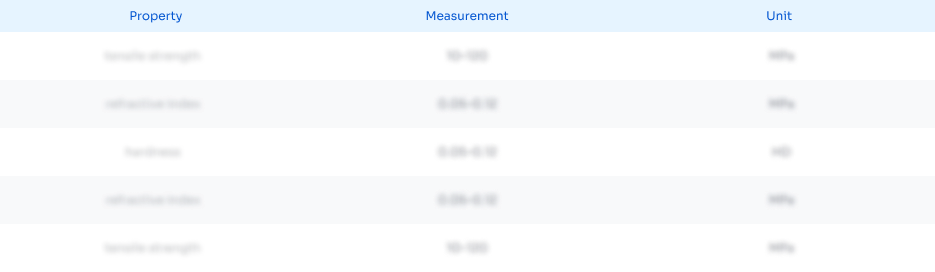
Abstract
Description
Claims
Application Information

- Generate Ideas
- Intellectual Property
- Life Sciences
- Materials
- Tech Scout
- Unparalleled Data Quality
- Higher Quality Content
- 60% Fewer Hallucinations
Browse by: Latest US Patents, China's latest patents, Technical Efficacy Thesaurus, Application Domain, Technology Topic, Popular Technical Reports.
© 2025 PatSnap. All rights reserved.Legal|Privacy policy|Modern Slavery Act Transparency Statement|Sitemap|About US| Contact US: help@patsnap.com