Method for degrading thermoplastic plastic polyethylene terephthalate
A polyethylene terephthalate and thermoplastic technology, which is applied in the field of polyester degradation, can solve the problems of unobtainable catalyst, polymetallic residue, long reaction time, etc. Effect
- Summary
- Abstract
- Description
- Claims
- Application Information
AI Technical Summary
Problems solved by technology
Method used
Image
Examples
Embodiment 1
[0063] Measure 2.48mL (5mmol) of trioctylphosphine, and add it into a 25mL pressure tube (the pressure tube has been dried beforehand); measure 3mL of methanol, mix and stir evenly; add 2.54mL (30mmol) of dimethyl carbonate. React at 140°C for 20 hours. After the reaction, excess dimethyl carbonate and by-product methanol can be removed by low-pressure rotary evaporation. The resulting salt was a colorless oily liquid (2.25 g, 98%), which 1 HNMR spectrum such as figure 1 shown. The deuterium reagent used is DMSO-d 6 , its chemical shift is 2.5, and the ratio of peak area is 3:6:3:6:6:24:9, which is in line with the expectation, and there is no obvious impurity peak. 1 H NMR and 13 C NMR ( figure 2 ) analysis can confirm that the structure of the catalyst (4c) is correct.
Embodiment 2
[0065] Measure 0.921g (2mmol) of the product in Example 1, add it into a 25mL eggplant-shaped bottle, weigh 0.2442g (2mmol) of benzoic acid and add it therein. The reaction was carried out at 50° C. for 2 h. After the reaction was over, the by-product methanol was removed by low-pressure rotary evaporation, and the main product was a colorless oily liquid (1.09 g, 98%). 1 HNMR spectrum such as image 3 shown. The deuterated reagent used is CDCl 3 , its chemical shift is 7.26, the ratio of peak area is 2:1:2:6:3:12:24:9, which is in line with the expectation, and there is no obvious miscellaneous peak. 1 H NMR and 13 C NMR ( Figure 4 ) analysis can confirm that the structure of the catalyst (4b) is correct.
[0066] Two, PET degradation reaction embodiment
Embodiment 3
[0068] Weigh BG80 PET 0.5g (W 0 ,N 0 =2.6mmol), put into a 10mL schlenk tube, measure 2.11mL of ethylene glycol, and 0.05g of catalyst 4c, and add them in sequence. Reaction at 180°C for 4h. After the reaction is over, weigh 0.1 g of the internal standard 1,3,5-trimethoxybenzene, add it directly to the reaction solution, stir for 30 minutes, and then take a sample. 1 According to H NMR analysis, the NMR yield of depolymerized monomer BHET was 87.93%. The reaction solution was filtered while it was hot, and the resulting filter cake was unreacted PET, which was washed 3 times with water at 70°C and dried in a vacuum oven for 12 hours, claiming its mass as 0.024g (W 1 ), the calculated PET degradation rate was 95.2%. The filtrate is BHET, oligomers, catalysts and ethylene glycol. Add 20mL of water to the filtrate and stir at 70°C for 30 minutes, then filter 3 times while it is hot, and place the filtrate directly in a refrigerator at 0°C for 24 hours. Monomer BHET crystalliz...
PUM
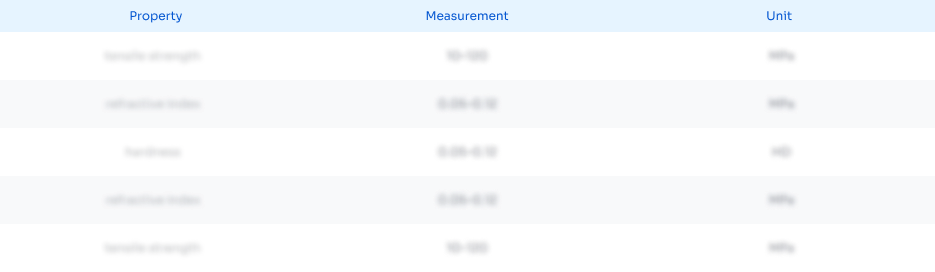
Abstract
Description
Claims
Application Information

- R&D
- Intellectual Property
- Life Sciences
- Materials
- Tech Scout
- Unparalleled Data Quality
- Higher Quality Content
- 60% Fewer Hallucinations
Browse by: Latest US Patents, China's latest patents, Technical Efficacy Thesaurus, Application Domain, Technology Topic, Popular Technical Reports.
© 2025 PatSnap. All rights reserved.Legal|Privacy policy|Modern Slavery Act Transparency Statement|Sitemap|About US| Contact US: help@patsnap.com