How to make pcb
A production method and technology of crimping holes, which are applied in the fields of printed circuit manufacturing, printed circuits, printed circuit components, etc., can solve the problems of increasing the thickness of finished PCBs, unfavorable insertion and installation of components, and uneven surface of PCBs, etc., to achieve improved Improve the quality, improve the flatness, and reduce the difficulty of PCB production
- Summary
- Abstract
- Description
- Claims
- Application Information
AI Technical Summary
Problems solved by technology
Method used
Image
Examples
Embodiment Construction
[0049] In order to describe the technical content, structural features, achieved objects and effects of the present invention in detail, the following detailed description is given in conjunction with the embodiments and the accompanying drawings.
[0050] see Figure 1-Figure 13 As shown, the PCB 100 of the present embodiment is manufactured by a manufacturing method of a PCB, and the manufacturing method of the PCB includes the following steps:
[0051] S1 , at least one crimping hole area 20 is formed on the sub-board 10 , and each crimping hole area 20 is provided with at least one crimping hole 30 .
[0052] It can be understood that the drawings involved in this embodiment are all illustrated with one of the crimping hole regions 20 of the PCB 100 , and the number of the crimping hole regions 20 of the PCB 100 may be one, two, three or four, etc. . The crimping hole area 20 is provided with a plurality of image 3 The shown crimping holes 30 penetrating the first surf...
PUM
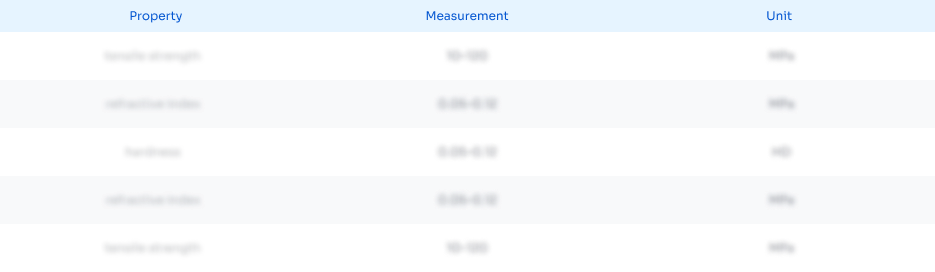
Abstract
Description
Claims
Application Information

- Generate Ideas
- Intellectual Property
- Life Sciences
- Materials
- Tech Scout
- Unparalleled Data Quality
- Higher Quality Content
- 60% Fewer Hallucinations
Browse by: Latest US Patents, China's latest patents, Technical Efficacy Thesaurus, Application Domain, Technology Topic, Popular Technical Reports.
© 2025 PatSnap. All rights reserved.Legal|Privacy policy|Modern Slavery Act Transparency Statement|Sitemap|About US| Contact US: help@patsnap.com