A constant force flexible grinding device for an industrial mechanical arm
An industrial machinery and flexible technology, applied in grinding drive devices, grinding automatic control devices, manufacturing tools, etc., can solve the problems of difficult to achieve industrial production, poor algorithm stability, slow response speed, etc., to improve grinding quality, torque, etc. Large, ensure the effect of grinding uniformity
- Summary
- Abstract
- Description
- Claims
- Application Information
AI Technical Summary
Problems solved by technology
Method used
Image
Examples
Embodiment 1
[0053] Such as Figure 1 to Figure 11 As shown, an industrial manipulator constant-force flexible grinding device includes a grinding head for grinding workpieces, a rotary motion component for driving the grinding head to rotate, an axial motion component for driving the grinding head to move axially, and a shaft for grinding. The flexible sleeve 10 for shock absorption in the direction and radial direction, as well as the internal components of the protection device and the outer casing 28 for bearing torque; the grinding device is connected to the mechanical arm through the flange 1 .
[0054] Axial moving parts include cylinder 3, upper end plate 2, lower end plate 7, thrust plate 18, linear bearing 21, floating joint 8, support rod 26, guide sleeve 29 and tension pressure sensor 9;
[0055] Rotary moving parts include air motor 25, motor mounting seat plate 30, coupling 24, ball spline, key 13 and rotary bearing 44; air motor 25 is installed on motor mounting seat plate 3...
Embodiment 2
[0064] An industrial mechanical arm constant force flexible grinding device, which is basically the same as Embodiment 1, the difference is that two cylinders 3 of the same type are used to provide the normal force during grinding, and the two cylinders 3 are symmetrically distributed about the air motor 25 The piston rod 5 of the cylinder 3 is connected to the thrust plate 18 through the floating joint 8, and the floating joint 8 can eliminate the vertical error of the connection between the thrust plate 18 and the piston rod 5, so that the cylinder 3 acts on the thrust plate 18 within a certain range of eccentricity. works fine. The air inlet A22 and the air inlet B27 of the cylinder 3 are respectively connected with an external electric proportional valve, and the air pressure of the air inlet A22 and the air inlet B27 can be precisely controlled by controlling the electric proportional valve. The air pressure of the air inlet A22 of the cylinder 3 is used for gravity compe...
PUM
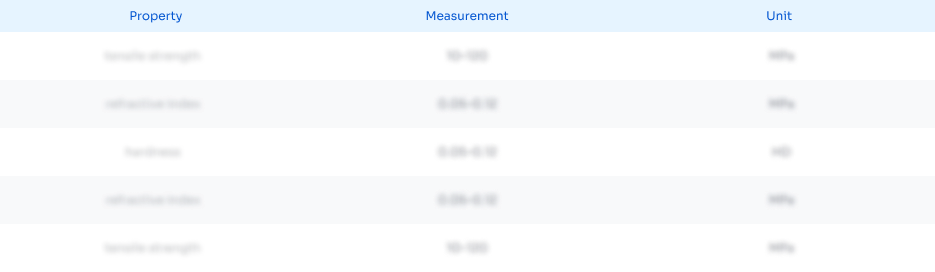
Abstract
Description
Claims
Application Information

- R&D Engineer
- R&D Manager
- IP Professional
- Industry Leading Data Capabilities
- Powerful AI technology
- Patent DNA Extraction
Browse by: Latest US Patents, China's latest patents, Technical Efficacy Thesaurus, Application Domain, Technology Topic, Popular Technical Reports.
© 2024 PatSnap. All rights reserved.Legal|Privacy policy|Modern Slavery Act Transparency Statement|Sitemap|About US| Contact US: help@patsnap.com