Automobile exhaust pipe welding forming post-processing equipment and post-processing method
A technology of welding forming and automobile exhaust, applied in welding equipment, auxiliary welding equipment, welding/cutting auxiliary equipment, etc., can solve the problems of low practicability, wear of exhaust pipe, and lack of grinding waste
- Summary
- Abstract
- Description
- Claims
- Application Information
AI Technical Summary
Problems solved by technology
Method used
Image
Examples
Embodiment Construction
[0033]In order to make the technical means, creative features, goals and effects achieved by the present invention easy to understand, the present invention will be further described below in conjunction with specific illustrations. It should be noted that, in the case of no conflict, the embodiments in the present application and the features in the embodiments can be combined with each other.
[0034] Such as Figure 1 to Figure 6 As shown, a post-processing equipment for automobile exhaust pipe welding and forming includes a base 1, a fixing device 2 and a grinding device 3. The lower end of the base 1 is connected to the existing ground, and the upper end of the base 1 is sequentially installed with Fixing device 2 and grinding device 3.
[0035] The fixing device 2 includes a support bracket 20, an annular plate 21, a fixed ring 22, a limit bolt 23, an arc block 24, a ring gear 25, an incomplete gear 26, a motor 27 and a motor seat 28, and the upper end of the base 1 Su...
PUM
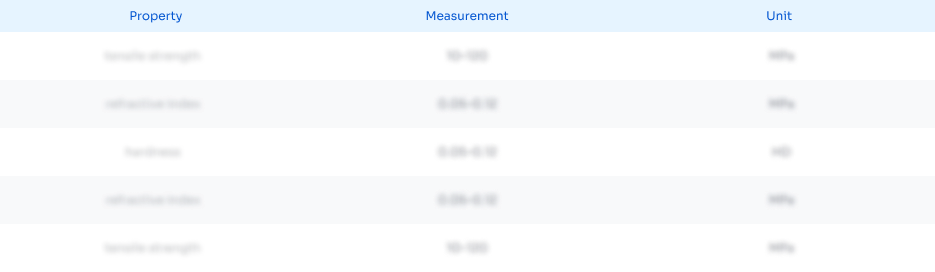
Abstract
Description
Claims
Application Information

- R&D
- Intellectual Property
- Life Sciences
- Materials
- Tech Scout
- Unparalleled Data Quality
- Higher Quality Content
- 60% Fewer Hallucinations
Browse by: Latest US Patents, China's latest patents, Technical Efficacy Thesaurus, Application Domain, Technology Topic, Popular Technical Reports.
© 2025 PatSnap. All rights reserved.Legal|Privacy policy|Modern Slavery Act Transparency Statement|Sitemap|About US| Contact US: help@patsnap.com