Preparation method and application of BiOCl/Fe-MOFs composite catalytic material
A catalytic material and reaction technology, used in organic compound/hydride/coordination complex catalysts, chemical instruments and methods, physical/chemical process catalysts, etc. The method is complex and other problems, to achieve the effect of fast preparation, simple preparation method and high purity
- Summary
- Abstract
- Description
- Claims
- Application Information
AI Technical Summary
Problems solved by technology
Method used
Image
Examples
Embodiment 1
[0030] Weigh 1.926g (9.69mmol) of ferrous chloride tetrahydrate and dissolve it in 97.2g deionized water, then add 0.539g (1.71mmol) of bismuth trichloride and dissolve it in the above solution to obtain mixed solution A, wherein bismuth ions account for The mole fraction of metal ions is 15%. Add 1.676g (7.6mmol) of trimesic acid into 23.72g of 1mol / L NaOH (22.8mmol) solution, heat to 60-70°C, stir and dissolve to obtain a clear solution B. Then solution B was slowly added dropwise to solution A at a rate of 0.5 mL / min, and the reaction was continued to stir at 30° C. at a rate of 400 r / min for 6 h. The resulting reaction mixture was left to stand, the supernatant was poured off, soaked in hot water and absolute ethanol, washed, and centrifuged several times, and then dried in a vacuum oven at 60°C to obtain the final BiOCl / Fe-MOFs composite catalytic material. figure 1 It is the SEM image of BiOCl / Fe-MOFs composite catalytic material.
Embodiment 2
[0032]Weigh 1.473g (7.41mmol) ferrous chloride tetrahydrate and dissolve in 97.2g deionized water, then add 1.528g (3.991mmol) of bismuth trichloride and dissolve in the above solution to obtain mixed solution A, wherein bismuth ions account for The mole fraction of metal ions is 35%. 1.676g (7.6mmol) of trimesic acid was added to 23.72g of 1mol / L NaOH (22.8mmol) solution, and heated to 60-70°C to obtain a clear solution B. Then solution B was slowly added dropwise to solution A at a rate of 0.3 mL / min, and continued to stir at 35° C. at a rate of 300 r / min for 6 h. The resulting reaction mixture was left standing, the supernatant was poured off, soaked in hot water and absolute ethanol, washed, centrifuged several times, and then dried in a vacuum oven at 60°C to obtain the final BiOCl / Fe-MOFs composite catalytic material.
Embodiment 3
[0034] Weigh 1.133g (5.70mmol) ferrous chloride tetrahydrate and dissolve it in 97.2g deionized water, then add 1.797g (5.70mmol) of bismuth trichloride and dissolve it in the above solution to obtain mixed solution A, wherein bismuth ions account for The mole fraction of metal ions is 50%. 1.676g (7.6mmol) of trimesic acid was added to 23.72g of 1mol / L NaOH (22.8mmol) solution, and heated to 60-70°C to obtain a clear solution B. Then solution B was slowly added dropwise to solution A at a rate of 0.6 mL / min, and continued to stir at 20° C. at a rate of 500 r / min for 6 h. The resulting reaction mixture was left standing, the supernatant was poured off, soaked in hot water and absolute ethanol, washed, centrifuged several times, and then dried in a vacuum oven at 60°C to obtain the final BiOCl / Fe-MOFs composite catalytic material.
PUM
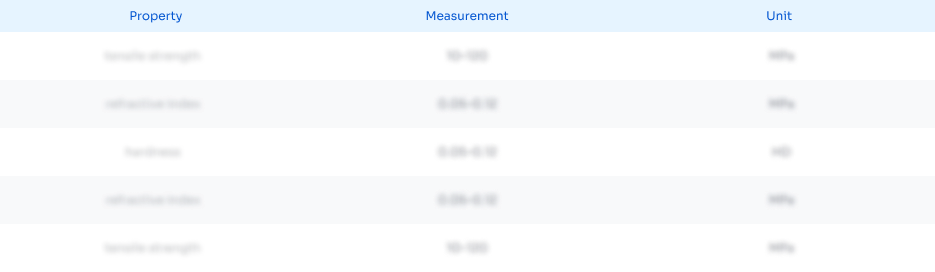
Abstract
Description
Claims
Application Information

- R&D
- Intellectual Property
- Life Sciences
- Materials
- Tech Scout
- Unparalleled Data Quality
- Higher Quality Content
- 60% Fewer Hallucinations
Browse by: Latest US Patents, China's latest patents, Technical Efficacy Thesaurus, Application Domain, Technology Topic, Popular Technical Reports.
© 2025 PatSnap. All rights reserved.Legal|Privacy policy|Modern Slavery Act Transparency Statement|Sitemap|About US| Contact US: help@patsnap.com