A method for preparing guaiacol and phenol by microwave-assisted depolymerization of lignin
A microwave-assisted, guaiacol technology, applied in the fields of biomass energy and chemicals, can solve the problems of low controllability of product components, high cost input, low yield of conversion products, etc., and achieves utilization value and economy. Good effect, reduce side reactions, improve heat transfer efficiency
- Summary
- Abstract
- Description
- Claims
- Application Information
AI Technical Summary
Problems solved by technology
Method used
Examples
Embodiment 1
[0039] 3g glycine and 15g Fe (NO 3 ) 3 ·7H 2 O was dissolved in 1000 mL of a mixture of ethanol and water (the volume ratio of ethanol and water was 1:2), hydrothermally reacted at 150 °C for 12 hours, cooled to room temperature, washed three times with ethanol and distilled water, and then dried at 50 °C Dry in the box for 8 hours to obtain Fe 2 O 3 Nanospheres; dissolve 1 g of alkali lignin in 1000 mL of tetrahydrofuran, then add 2 g of Fe obtained above 2 O 3 Nanospheres, after fully stirring for 3 hours, placed in a dialysis bag with a molecular weight cut-off of 8000, put the dialysis bag into deionized water, and slowly stirred and dialyzed in a fume hood for 24 hours to obtain core-shell Fe 2 O 3 @Lignin was washed 4 times with absolute ethanol and dried at 100 °C for 12 h to obtain dry core-shell Fe 2 O 3 @Lignin; add 1g ammonium molybdate and 5g thiourea to 150mL deionized water and mix well, stir at 60°C for 6 hours, add oxalic acid, adjust pH to 2, take the ...
Embodiment 2
[0041] 3g glycine and 30g Fe (NO 3 ) 3 ·7H 2 O was dissolved in 500 mL of a mixture of ethanol and water (the volume ratio of ethanol and water was 1:2), hydrothermally reacted at 180 °C for 12 hours, cooled to room temperature, washed with ethanol and distilled water for 4 times, and then dried at 80 °C Dry in the box for 6 hours to obtain Fe 2 O 3 Nanospheres; dissolve 1 g of solvent lignin in 200 mL of tetrahydrofuran, then add 0.5 g of Fe obtained above 2 O 3 Nanospheres, after fully stirring for 3 hours, placed in a dialysis bag with a molecular weight cut-off of 14,000, put the dialysis bag into deionized water, and slowly stirred and dialyzed in a fume hood for 36 hours to obtain core-shell Fe 2 O 3 @Lignin was washed 6 times with absolute ethanol and dried at 80 °C for 12 h to obtain dry core-shell Fe 2 O 3 @Lignin; add 1 g of ammonium molybdate and 2 g of thiourea into 80 mL of deionized water and mix well, stir at 50°C for 6 hours, add oxalic acid, adjust the...
Embodiment 3
[0043] 3g glycine and 24g Fe (NO 3 ) 3 ·7H 2 O was dissolved in 750 mL of a mixture of ethanol and water (the volume ratio of ethanol and water was 1:2), hydrothermally reacted at 200 °C for 12 hours, cooled to room temperature, washed with ethanol and distilled water for 5 times, and then dried at 60 °C Dry in the box for 7 hours to obtain Fe 2 O 3 Nanospheres; 1 g of sulfated lignin was dissolved in 500 mL of tetrahydrofuran, and then 1 g of Fe obtained above was added 2 O 3 Nanospheres, after fully stirring for 3 hours, placed in a dialysis bag with a molecular weight cut-off of 10,000, put the dialysis bag into deionized water, and slowly stirred and dialyzed in a fume hood for 48 hours to obtain core-shell Fe 2 O 3 @Lignin was washed 5 times with absolute ethanol and dried at 90 °C for 12 h to obtain dry core-shell Fe 2 O 3 @Lignin; add 1g ammonium molybdate and 3g thiourea to 100mL deionized water and mix well, stir at 40°C for 6 hours, add oxalic acid, adjust pH...
PUM
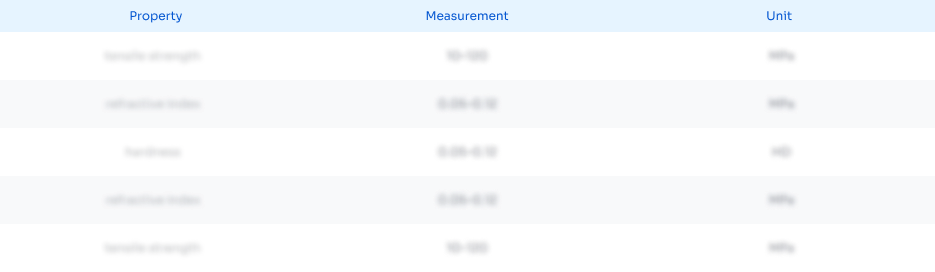
Abstract
Description
Claims
Application Information

- R&D
- Intellectual Property
- Life Sciences
- Materials
- Tech Scout
- Unparalleled Data Quality
- Higher Quality Content
- 60% Fewer Hallucinations
Browse by: Latest US Patents, China's latest patents, Technical Efficacy Thesaurus, Application Domain, Technology Topic, Popular Technical Reports.
© 2025 PatSnap. All rights reserved.Legal|Privacy policy|Modern Slavery Act Transparency Statement|Sitemap|About US| Contact US: help@patsnap.com