Case panel machining method
A technology for a chassis panel and a processing method, applied in the field of mechanical processing, can solve the problems of unstable and unsafe thick plates, empty strokes in planing processing, low production efficiency, etc., and achieves easy guarantee of dimensional accuracy, compact production process, and production cycle. short effect
- Summary
- Abstract
- Description
- Claims
- Application Information
AI Technical Summary
Problems solved by technology
Method used
Image
Examples
Embodiment Construction
[0030] The technical solution of the present invention is further described below, but the scope of protection is not limited to the description.
[0031] like figure 1 as shown, figure 1 It is a structural schematic diagram of the finished chassis panel to be processed. The panel is 482.6mm long, 177mm wide, and 12mm in total thickness. The panel is provided with a rectangular ring-shaped flange to form a 5.5mm thick step. In addition, there are mounting holes for installing components and cavity. In the figure: the first stepped surface 1, the second stepped surface 2, the third stepped surface 3, the fourth stepped surface 4, and the four stepped surfaces are located on a plane.
[0032] The processing steps are mainly two parts: blanking and CNC milling:
[0033] Blanking: wire cutting electric machining blanking, cutting the 2A12-H112 high-strength hard aluminum alloy rolled plate into a cuboid blank with a size of 490mm×190mm×15mm, so that the grain direction of the p...
PUM
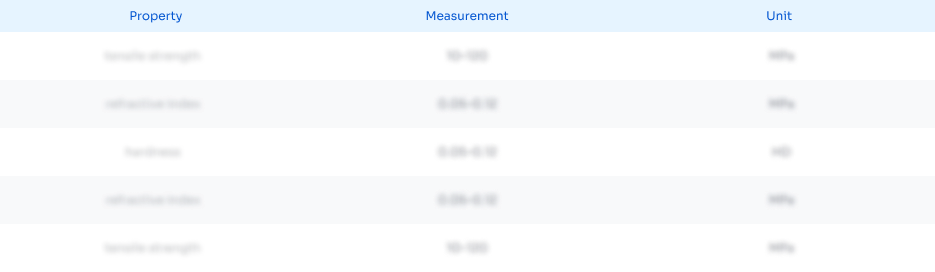
Abstract
Description
Claims
Application Information

- R&D
- Intellectual Property
- Life Sciences
- Materials
- Tech Scout
- Unparalleled Data Quality
- Higher Quality Content
- 60% Fewer Hallucinations
Browse by: Latest US Patents, China's latest patents, Technical Efficacy Thesaurus, Application Domain, Technology Topic, Popular Technical Reports.
© 2025 PatSnap. All rights reserved.Legal|Privacy policy|Modern Slavery Act Transparency Statement|Sitemap|About US| Contact US: help@patsnap.com