Improved current prediction control method of switched reluctance motor
A technology of switched reluctance motor and control method, which is applied in the direction of motor generator control, AC motor control, electronic commutation motor control, etc., and can solve the problems of lacking, ignoring the nonlinear characteristics of switched reluctance motor, and the control is not delicate, etc. Achieve the effects of reducing current overshoot, realizing high-performance operation, and reducing the amount of calculation
- Summary
- Abstract
- Description
- Claims
- Application Information
AI Technical Summary
Problems solved by technology
Method used
Image
Examples
Embodiment Construction
[0045] The specific embodiment of the present invention is as figure 1 As shown, the microcontroller 1 is STM32F030C6, and the power converter 3 adopts a three-phase asymmetrical half-bridge structure. The switched reluctance motor is a 12 / 8-pole three-phase switched reluctance motor 2 with a rated speed of 2200r / min. It is powered by a power converter 3, and the current is detected by a current sensor and a current detection filter circuit 5, and is input to the microcontroller The ADC0 port of the device 1, the position detection unit 6 (position sensor) is composed of the rotor position measurement tooth disc, two slot-type Hall switch devices and corresponding circuits. Microcontroller 1 obtains the state of the two Hall switches by inputting the capture interrupt to determine the current position of the rotor.
[0046] The switched reluctance motor adopts double closed-loop control of speed and current. The actual speed of the motor and the current position of the rotor...
PUM
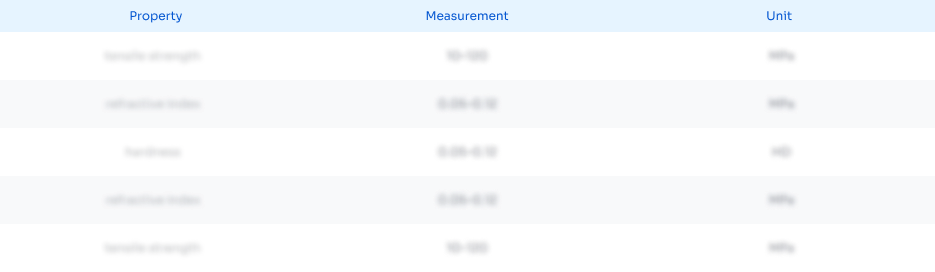
Abstract
Description
Claims
Application Information

- R&D
- Intellectual Property
- Life Sciences
- Materials
- Tech Scout
- Unparalleled Data Quality
- Higher Quality Content
- 60% Fewer Hallucinations
Browse by: Latest US Patents, China's latest patents, Technical Efficacy Thesaurus, Application Domain, Technology Topic, Popular Technical Reports.
© 2025 PatSnap. All rights reserved.Legal|Privacy policy|Modern Slavery Act Transparency Statement|Sitemap|About US| Contact US: help@patsnap.com