High-performance composite dielectric filter, material thereof, and preparation method of material
A composite medium and high-performance technology, applied in the direction of waveguide devices, resonators, electrical components, etc., can solve the problems of low production efficiency, high production cost, cracking of components, etc., to reduce industrial energy consumption and production costs, improve Production efficiency, the effect of not easy to crack
- Summary
- Abstract
- Description
- Claims
- Application Information
AI Technical Summary
Problems solved by technology
Method used
Image
Examples
preparation example Construction
[0029] The invention discloses a preparation method of a high-performance composite dielectric filter material, which includes the following steps:
[0030] (1) Weighing: Take ceramic powder with a dielectric constant of 40-120, and its mass percentage is 40%-70%.
[0031] (2) Mixing: Mix ceramic powder, deionized water, and dispersant in a weight ratio of 1:1:0.005 to obtain a mixture. The type of dispersant is SF8.
[0032] (3) Ball milling: Pour the above mixture into a circulating stirring ball mill barrel with φ6mm grinding balls and grind for 8 hours, and the particle size of the slurry after grinding is less than 0.6 μm.
[0033] (4) Drying: Use a centrifugal spray drying tower with an induced air temperature of 100±5°C, a supply air temperature of 250±5°C, an atomizing disc rotation speed of 22Hz, and a feeding speed of 40Hz to dry the slurry to obtain powder.
[0034] (5) Pre-firing: Put the powder obtained in step (4) into an alumina crucible, circulate the tunnel k...
Embodiment 1
[0047] (1) Weighing: Take ceramic powder with a dielectric constant of 40, and its mass percentage is 45%.
[0048] (2) Mixing: Mix ceramic powder, deionized water, and dispersant in a weight ratio of 1:1:0.005 to obtain a mixture. The type of dispersant is SF8.
[0049] (3) Ball milling: Pour the above mixture into a circulating stirring ball mill barrel with φ6mm grinding balls and grind for 8 hours, and the particle size of the slurry after grinding is less than 0.6 μm.
[0050] (4) Drying: Use a centrifugal spray drying tower with an induced air temperature of 100°C, a supply air temperature of 250°C, an atomization disc rotation speed of 22Hz, and a feeding speed of 40Hz to dry the slurry to obtain powder.
[0051] (5) Pre-firing: Put the powder obtained in step (4) into an alumina crucible, circulate the tunnel kiln temperature at 1330°C, and work for 4 hours.
[0052] (6) Pulverization: The material obtained in step (5) is pulverized and passed through a 100-mesh sieve...
Embodiment 2
[0060] (1) Weighing: Take ceramic powder with a dielectric constant of 40-120, and its mass percentage is 43%.
[0061] (2) Mixing: Mix ceramic powder, deionized water, and dispersant in a weight ratio of 1:1:0.005 to obtain a mixture. The type of dispersant is SF8.
[0062] (3) Ball milling: Pour the above mixture into a circulating stirring ball mill barrel with φ6mm grinding balls and grind for 8 hours, and the particle size of the slurry after grinding is less than 0.6 μm.
[0063] (4) Drying: Use a centrifugal spray drying tower with an induced air temperature of 100°C, a supply air temperature of 250°C, an atomization disc rotation speed of 22Hz, and a feeding speed of 40Hz to dry the slurry to obtain powder.
[0064] (5) Pre-firing: Put the powder obtained in step (4) into an alumina crucible, circulate the tunnel kiln temperature at 1330°C, and work for 4 hours.
[0065] (6) Pulverization: The material obtained in step (5) is pulverized and passed through a 100-mesh s...
PUM
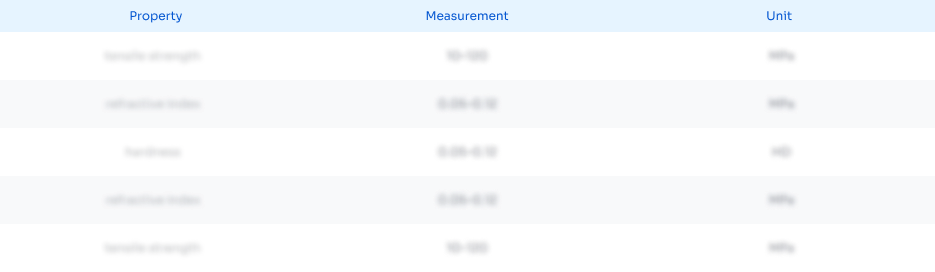
Abstract
Description
Claims
Application Information

- R&D Engineer
- R&D Manager
- IP Professional
- Industry Leading Data Capabilities
- Powerful AI technology
- Patent DNA Extraction
Browse by: Latest US Patents, China's latest patents, Technical Efficacy Thesaurus, Application Domain, Technology Topic, Popular Technical Reports.
© 2024 PatSnap. All rights reserved.Legal|Privacy policy|Modern Slavery Act Transparency Statement|Sitemap|About US| Contact US: help@patsnap.com