Dry powder brick pressing preparation method of lithium ion battery pole piece
A lithium-ion battery and pole piece technology, which is applied in battery electrodes, electrode manufacturing, batteries, etc., can solve the problems of ion battery pole piece burrs, poor consistency of film layer compaction density, and high investment costs, so as to avoid inconsistent coating thickness. , The effect of solving the difficulty of slurry transportation and solving the problem of precipitation and agglomeration
- Summary
- Abstract
- Description
- Claims
- Application Information
AI Technical Summary
Problems solved by technology
Method used
Image
Examples
Embodiment
[0031]
[0032] Assemble the positive electrode material, negative electrode material and separator: Celgard 2400 into a pouch battery, using the electrolyte: 1MLiPF 6 +EC: DEC = 1:1 (volume ratio), the electrochemical performance test was carried out on the blue electric battery tester, a total of 6 groups of parallel tests were set up, and the battery performance results are as follows:
[0033] serial number 800 cycles at room temperature Capacity retention % 45°C cycle 800 times capacity retention % Soft pack battery 1 92 90 Soft pack battery 2 93 91 Soft pack battery 3 92 91 Soft pack battery 4 92 90 Soft pack battery 5 95 92 Soft pack battery 6 94 91
PUM
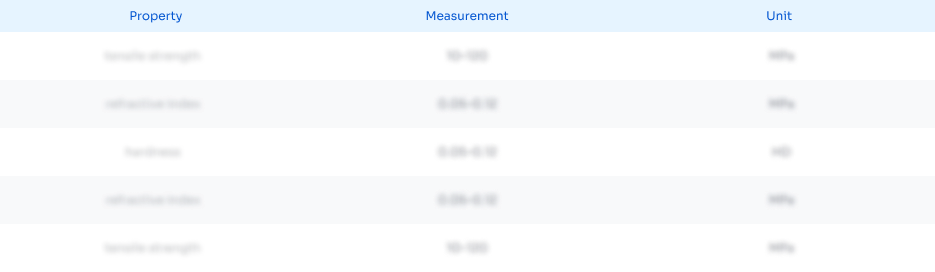
Abstract
Description
Claims
Application Information

- R&D
- Intellectual Property
- Life Sciences
- Materials
- Tech Scout
- Unparalleled Data Quality
- Higher Quality Content
- 60% Fewer Hallucinations
Browse by: Latest US Patents, China's latest patents, Technical Efficacy Thesaurus, Application Domain, Technology Topic, Popular Technical Reports.
© 2025 PatSnap. All rights reserved.Legal|Privacy policy|Modern Slavery Act Transparency Statement|Sitemap|About US| Contact US: help@patsnap.com