Method for eliminating residual stress of titanium part subjected to powerful spinning deformation
A powerful spinning and residual stress technology, applied in the field of residual stress relief of titanium parts, can solve problems such as adverse effects on performance, decreased performance of materials, incomplete stress release, etc., to improve overall quality and performance, and prolong work. Longevity, effect of reducing the risk of deformation
- Summary
- Abstract
- Description
- Claims
- Application Information
AI Technical Summary
Problems solved by technology
Method used
Image
Examples
Embodiment 1
[0024] A method for eliminating residual stress of a titanium part deformed by strong spinning, comprising the following steps:
[0025] Step 1: Place the spun titanium parts in a vacuum of 10 -2 GPa~10 -4 In the GPa heat treatment furnace, the temperature is raised to the target temperature of 560°C (recrystallization temperature range) at a heating rate of 50°C / min, and the holding time is 60min; the deformation residual stress inside the part is fully eliminated;
[0026] Step 2: After heat preservation, cool (slowly cool) to 400°C by cooling with the furnace, and then take out the furnace and air cool to room temperature; in order to eliminate the influence of thermal stress generated during the cooling process.
Embodiment 2
[0028] The difference from Example 1 is that the sample is directly taken out of the furnace for air cooling.
Embodiment 3
[0030] The difference from Example 1 is that the heating rate is 30°C / min, the target temperature is 530°C, the holding time is 80min, and the furnace is cooled to 410°C.
PUM
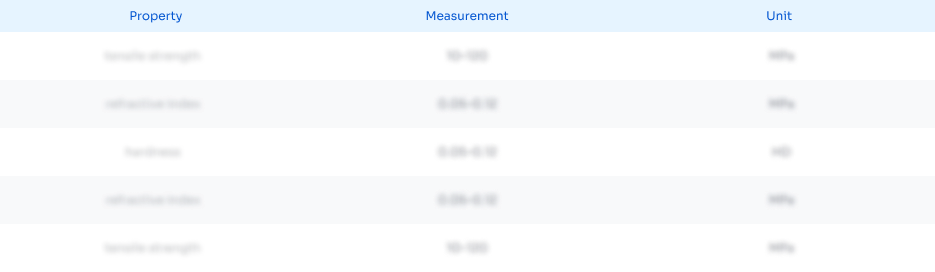
Abstract
Description
Claims
Application Information

- R&D
- Intellectual Property
- Life Sciences
- Materials
- Tech Scout
- Unparalleled Data Quality
- Higher Quality Content
- 60% Fewer Hallucinations
Browse by: Latest US Patents, China's latest patents, Technical Efficacy Thesaurus, Application Domain, Technology Topic, Popular Technical Reports.
© 2025 PatSnap. All rights reserved.Legal|Privacy policy|Modern Slavery Act Transparency Statement|Sitemap|About US| Contact US: help@patsnap.com