Hyperspectral display frame hyperspectral traceless injection molding technique
An injection molding process, high-gloss and traceless technology, applied in the field of injection molding, can solve the problems of heating and cooling affecting appearance, low qualified rate of finished products, low production efficiency, etc.
- Summary
- Abstract
- Description
- Claims
- Application Information
AI Technical Summary
Problems solved by technology
Method used
Examples
Embodiment 1
[0023] A high-gloss traceless injection molding process for a high-gloss display frame of the present invention comprises the following steps:
[0024] (1) Mold opening: Design the corresponding injection mold according to the structure of the display frame product, and the mold is equipped with a follow-up water channel close to the cavity, and the mold is manufactured and processed in strict accordance with the mold design drawings, and the mold is tested after the mold is completed Subsequent processes can only be carried out after passing the test;
[0025] (2) Material selection and processing: choose PC, PC / PMMA, PMMA / ABS, high-gloss ABS material or PC / GF with good fluidity as injection molding material, and place the selected injection molding material in a vacuum condensation box for 5-10 After condensation treatment at ℃ for 0.5-1.0h, put it into a vacuum drying oven and dry at 80-90℃ for 2-3h to make the humidity less than 0.2%. Finally, microwave the injection moldi...
Embodiment 2
[0037] A high-gloss traceless injection molding process for a high-gloss display frame of the present invention comprises the following steps:
[0038] (1) Mold opening: Design the corresponding injection mold according to the structure of the display frame product, and the mold is equipped with a follow-up water channel close to the cavity, and the mold is manufactured and processed in strict accordance with the mold design drawings, and the mold is tested after the mold is completed Subsequent processes can only be carried out after passing the test;
[0039] (2) Material selection and processing: choose PC, PC / PMMA, PMMA / ABS, high-gloss ABS material or PC / GF with good fluidity as injection molding material, and place the selected injection molding material in a vacuum condensation box for 5-10 After condensation treatment at ℃ for 0.5-1.0h, put it into a vacuum drying oven and dry at 80-90℃ for 2-3h to make the humidity less than 0.2%. Finally, microwave the injection moldi...
PUM
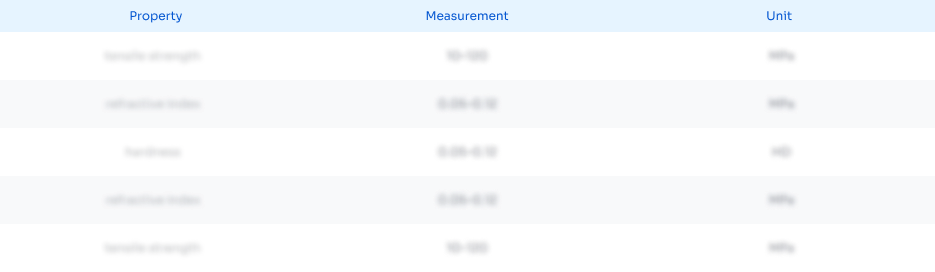
Abstract
Description
Claims
Application Information

- Generate Ideas
- Intellectual Property
- Life Sciences
- Materials
- Tech Scout
- Unparalleled Data Quality
- Higher Quality Content
- 60% Fewer Hallucinations
Browse by: Latest US Patents, China's latest patents, Technical Efficacy Thesaurus, Application Domain, Technology Topic, Popular Technical Reports.
© 2025 PatSnap. All rights reserved.Legal|Privacy policy|Modern Slavery Act Transparency Statement|Sitemap|About US| Contact US: help@patsnap.com