Preparation method and application of zinc oxide high polymer
A high-polymer, zinc oxide technology, applied in pharmaceutical formulations, dental preparations, mold cups, etc., can solve the problems of easy agglomeration of nano-zinc oxide and hindering application efficiency.
- Summary
- Abstract
- Description
- Claims
- Application Information
AI Technical Summary
Problems solved by technology
Method used
Image
Examples
Embodiment 1
[0027] A preparation method of zinc oxide polymer, comprising the following steps:
[0028] 1) In an anhydrous and oxygen-free environment, 18Kg Zn(NO 3 ) 2 ·6H 2 O was dissolved in 200L of anhydrous methanol. After complete dissolution, 0.9 Kg of urea and 39 Kg of benzyl alcohol were added to the mixture. Under nitrogen atmosphere, after stirring in the autoclave for 6 hours, the temperature was raised to 200° C. for 10 hours, and then heated to 280° C. for 5 hours to remove internal low boilers. Centrifuge to collect the dry gray powder, then calcinate to 600°C at a heating rate of 5°C / min, and then keep at 600°C for 6h to prepare nano-zinc oxide carrier particles with many defects on the surface.
[0029] 2) Add 4000g of nano-zinc oxide carrier particles prepared in step 1) and 1000g of anhydrous magnesium chloride into a dry and sealed ball mill jar replaced by high-purity nitrogen three times under a nitrogen atmosphere, and then inject 15mL of analytically pure titan...
Embodiment 2
[0032] A preparation method of zinc oxide polymer, comprising the following steps:
[0033] 1) In an anhydrous and oxygen-free environment, 18Kg Zn(NO 3 ) 2 ·6H 2 O was dissolved in 200L of anhydrous methanol. After complete dissolution, 0.9 Kg of urea and 39 Kg of benzyl alcohol were added to the mixture. Under nitrogen atmosphere, after stirring in the autoclave for 6 hours, the temperature was raised to 200° C. for 10 hours, and then heated to 280° C. for 5 hours to remove internal low boilers. Centrifuge to collect the dry gray powder, then calcinate to 600°C at a heating rate of 5°C / min, and then keep at 600°C for 6h to prepare nano-zinc oxide carrier particles with many defects on the surface.
[0034] 2) Add 4000g of nano-zinc oxide carrier particles prepared in step 1) and 1000g of anhydrous magnesium chloride into a dry and sealed ball mill jar replaced by high-purity nitrogen three times under a nitrogen atmosphere, and then inject 15mL of analytically pure titan...
Embodiment 3
[0037] A preparation method of zinc oxide polymer, comprising the following steps:
[0038] 1) In an anhydrous and oxygen-free environment, 18Kg Zn(NO 3 ) 2 ·6H 2 O was dissolved in 200L of anhydrous methanol. After complete dissolution, 0.9 Kg of urea and 39 Kg of benzyl alcohol were added to the mixture. Under nitrogen atmosphere, after stirring in the autoclave for 6 hours, the temperature was raised to 200° C. for 10 hours, and then heated to 280° C. for 5 hours to remove internal low boilers. Centrifuge to collect the dry gray powder, then calcinate to 600°C at a heating rate of 5°C / min, and then keep at 600°C for 6h to prepare nano-zinc oxide carrier particles with many defects on the surface.
[0039] 2) Add 4000g of nano-zinc oxide carrier particles prepared in step 1) and 1000g of anhydrous magnesium chloride into a dry and sealed ball mill jar replaced by high-purity nitrogen three times under a nitrogen atmosphere, and then inject 15mL of analytically pure titan...
PUM
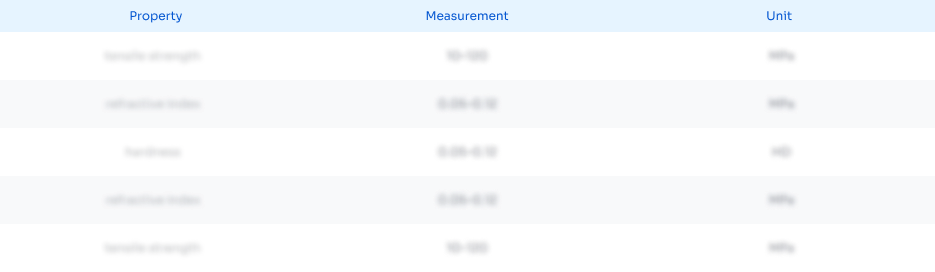
Abstract
Description
Claims
Application Information

- R&D Engineer
- R&D Manager
- IP Professional
- Industry Leading Data Capabilities
- Powerful AI technology
- Patent DNA Extraction
Browse by: Latest US Patents, China's latest patents, Technical Efficacy Thesaurus, Application Domain, Technology Topic, Popular Technical Reports.
© 2024 PatSnap. All rights reserved.Legal|Privacy policy|Modern Slavery Act Transparency Statement|Sitemap|About US| Contact US: help@patsnap.com