Thermoplastic composite fiber preform and forming method thereof
A composite material fiber and molding method technology, which is applied to heating/cooling fabrics, textiles, fabrics, etc., can solve the problems of large fluctuations in resin content of composite materials, difficult molding, and high resin viscosity, and achieves good apparent quality and enhanced impregnation. effect of effect
- Summary
- Abstract
- Description
- Claims
- Application Information
AI Technical Summary
Problems solved by technology
Method used
Image
Examples
Embodiment Construction
[0020] see below figure 1 , the present invention will be further described in conjunction with specific embodiments, but the content of the present invention is not limited to the following embodiments.
[0021] A fiber prefabricated body of thermoplastic composite material and its molding method, characterized in that the composite material is formed by thermocompression of a fabric prefabricated body, and the fabric prefabricated body is a three-layer fabric, which is woven from four systems of warp yarns and three systems of weft yarns. become. Among them, four warp yarn systems are composed of upper layer warp yarn 1.1, inner layer warp yarn 2.1, lower layer warp yarn 3.1 and binding warp yarn 4.1; three weft yarn systems are composed of upper layer weft yarn 1.2, inner layer weft yarn 2.2 and lower layer weft yarn 3.2; upper layer warp yarn 1.1 and upper layer The weft yarn 1.2 interweaves to form the upper layer fabric 1, the inner layer warp yarn 2.1 and the inner lay...
PUM
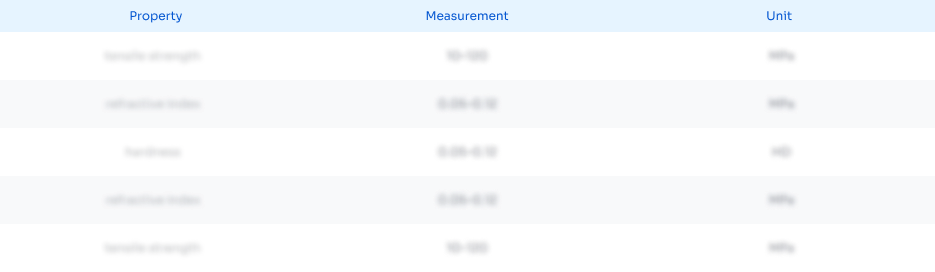
Abstract
Description
Claims
Application Information

- R&D
- Intellectual Property
- Life Sciences
- Materials
- Tech Scout
- Unparalleled Data Quality
- Higher Quality Content
- 60% Fewer Hallucinations
Browse by: Latest US Patents, China's latest patents, Technical Efficacy Thesaurus, Application Domain, Technology Topic, Popular Technical Reports.
© 2025 PatSnap. All rights reserved.Legal|Privacy policy|Modern Slavery Act Transparency Statement|Sitemap|About US| Contact US: help@patsnap.com